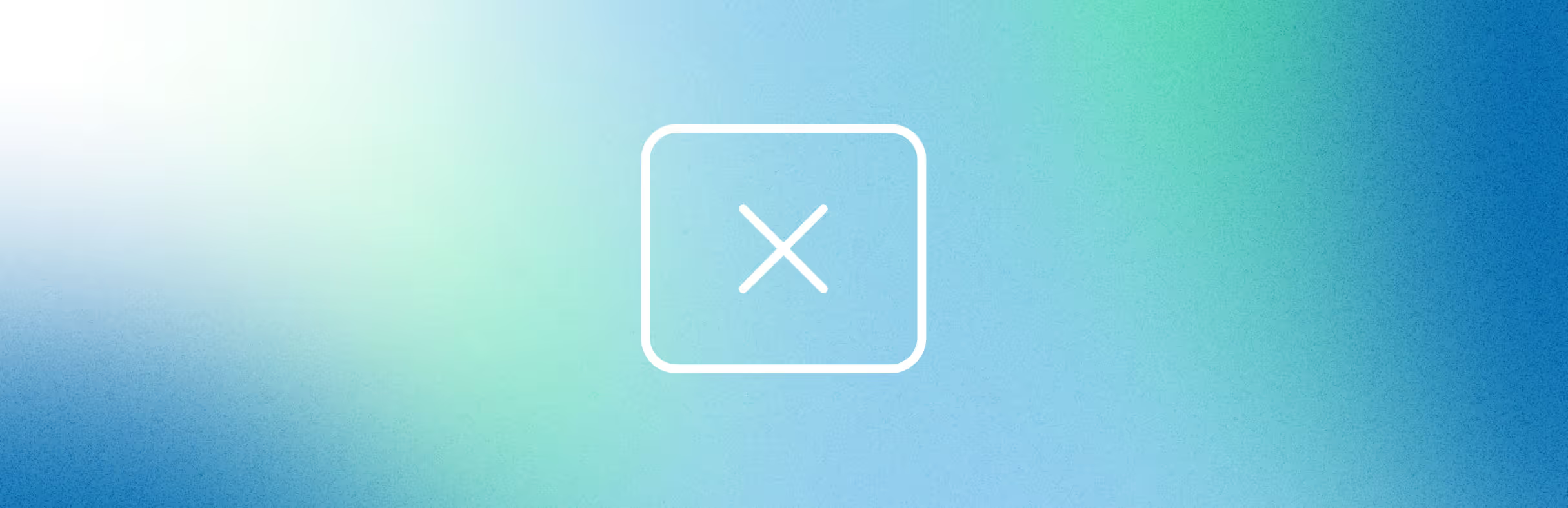
Just as we care for our bodies with preventive healthcare practices, the equipment also requires special attention to circumvent deterioration and damage over time. But alarmingly, most of today’s facilities managers still follow an “if ain’t broke, don’t fix it style of management, which rarely pays off in the long run. Simply put, solely relying on deferred maintenance leaves these facilities vulnerable to lost productivity and added costs.
This is where preventive maintenance shifts the paradigm.
Performing regular preventive maintenance ensures the efficiency of your facility and provides the peace of mind to keep your enterprise running smoothly. The mean time between failures (MTBF) is a KPI that facilitates planning preventive maintenance at the most suitable time for averting equipment breakdown.
Understanding MTBF
MTBF is the average of the duration between failures or breakdowns of mission-critical mechanics and technological systems. It was pioneered by the aviation industry as a yardstick for reliability and safety. Over the years, the metric has gained popularity across industries due to its ability to predict system downtimes. Measured in hours, its value enables facility managers prioritize unplanned maintenance and determine potential uptime, equipment reliability, and asset life expectancy. The primary goal of MTBF is to enable enterprises to maximize operations without disruptions with increased the time between failures. This keeps inspections and preventive maintenance tasks out of the equation as long as possible.
Benefits of MTBF on enterprise predictive maintenance strategies
For enterprises, implementing a predictive maintenance strategy that centers around increasing MTBF comes with a slew of benefits. These include, but are not limited to:
Optimizing schedules for maintenance
MTBF can help enterprises optimize their predictive maintenance schedules by providing a baseline. This enables leadership teams to plan maintenance tasks before the occurrence of any failure, allowing technicians to carry out condition-based maintenance when required.
Boosting MRO inventory
By tracking MTBF, managers can efficiently do inventory purchasing for MRO and ensure that every required piece of hardware is always available. Accurate tracking of MTBF provides an timely prediction for when required replacement parts will be needed. This lowers repair costs, increases liquid capital, and reduces repair times.
Identifying high-risk equipment
By accurately calculating the MTBF of various equipment, managers can identify the assets that are at a higher risk of failure and prioritize maintenance activities accordingly.
Reducing downtime
Predictive maintenance strategies that focus on increasing MTBF help organizations identify potential issues before they turn into major problems. They are also effective in forecasting the suitable time for conducting maintenance activities, ensuring minimum equipment downtime.
Forecasting failures
With MTBF, managers can predict the frequency of failures during production by calculating the average time between failures of equipment, systems, or components by leveraging historical failure data
TMA Systems: Propelling your predictive maintenance strategy to the next level
Collaborating with a suitable service provider is critical for developing an effective preventive maintenance strategy for your enterprise.
TMA Systems can be a partner of choice for all of your maintenance management needs. We are a leading technology company that provides a suite of advanced tools and services, including data migration, implementation and support. Our solutions seamlessly integrate with multiple systems, including ERP, to help you improve data quality and collection for effective and efficient maintenance practices.
To learn more about how TMA Systems can improve your mean time between failures (MTBF) and streamline your organizational processes, schedule a demo today.
Ready for a Demo?
Interested in taking this to the next level? Sign up for a free demo with a TMA Systems Account Executive. Enter your email below and we will reserve a time for you to test drive WebTMA.
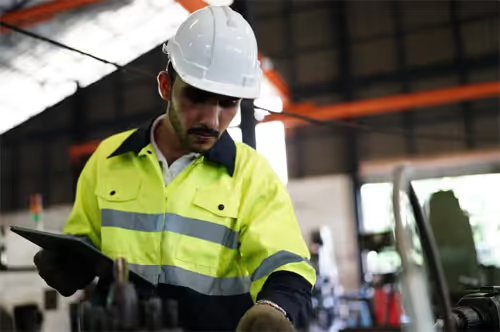
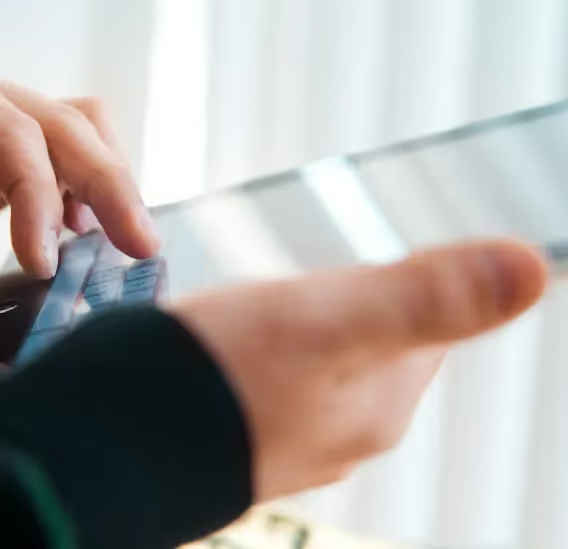
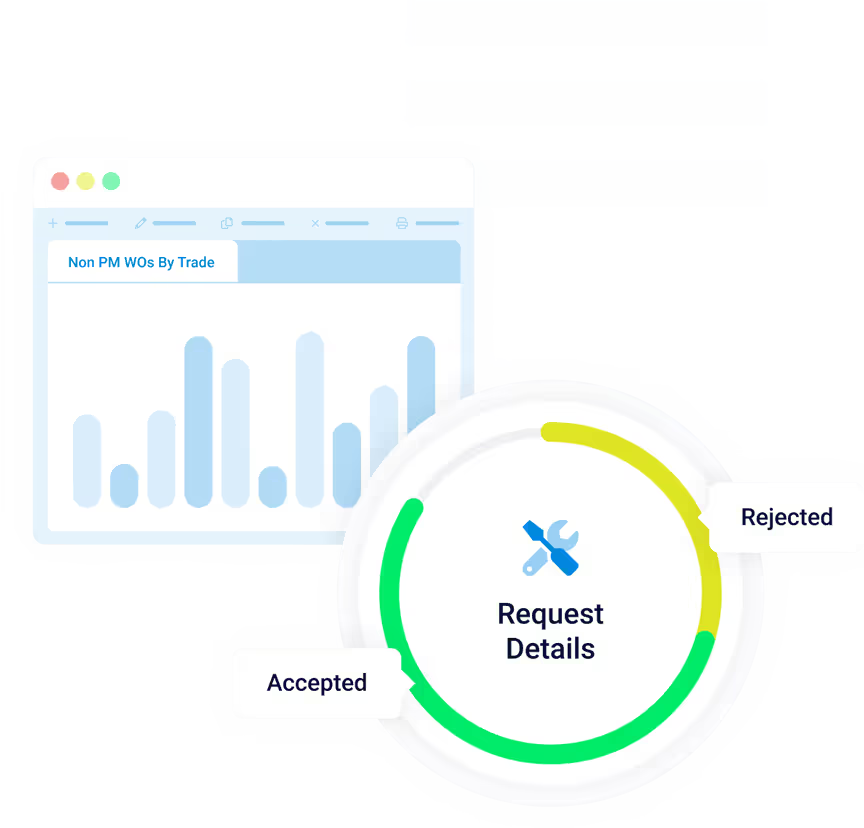