The Importance of Preventive Maintenance
A preemptive maintenance approach to maintaining equipment and facilities, preventive maintenance involves regularly scheduled inspections, tests, and other service activities. The primary aim is to identify and correct potential problems before they can cause frustration and failures.
A few key benefits of implementing a preventive maintenance program:
- Increase equipment reliability and availability: Identify and correct potential problems before they cause failures. A preventive maintenance strategy can help ensure that equipment is always available and operating at its optimal level reducing downtime and improving productivity.
- Reduce repair costs: Minimize the need for costly repairs by analyzing and addressing potential problems before they become major issues. This can be a significant long-term cost-savings for organizations.
- Improve safety: Protect workers and boost overall safety in the workplace. Regularly scheduled inspections and maintenance activities can help to pinpoint and correct safety hazards before they cause accidents or injuries.
- Extend equipment lifespan: Increase the lifespan of equipment and reduce the need for replacements. Preventive maintenance can help lower associated costs of replacing physical assets.
- Improve compliance: Ensure compliance with accurate reporting and equipment upkeep. Many organizations are required to follow specific maintenance and safety regulations that, if ignored, can have potential fines or penalties.
The predictive maintenance market is expected to grow to $17.09 billion in 2026 at a compound annual growth rate (CAGR) of 30.67%.
Different Types of Preventive Maintenance
There are many types of preventive maintenance. The most appropriate kind for a given situation will depend on the equipment, the environment in which it is used, and other factors. Organizations may use a combination of preventive maintenance strategies to ensure that their equipment is properly maintained and operating at peak efficiency. Some of the most common types include:
- Time-based maintenance is performed at regular intervals, regardless of the condition of the equipment. This approach is often used when the equipment manufacturer recommends specific timelines for maintenance activities, like replacing filters or lubricating moving parts.
- Condition-based maintenance is based on the condition of the equipment. This type of maintenance is performed when the equipment shows signs of wear or degradation, caused by activities like increased vibration or temperature. This can also be used when equipment sensors or other monitoring systems indicate that maintenance is needed.
- Predictive maintenance is based on data and analytics. This method uses data from sensors and other equipment monitoring systems to predict when maintenance is needed, prioritizing maintenance activities based on the likelihood of failure.
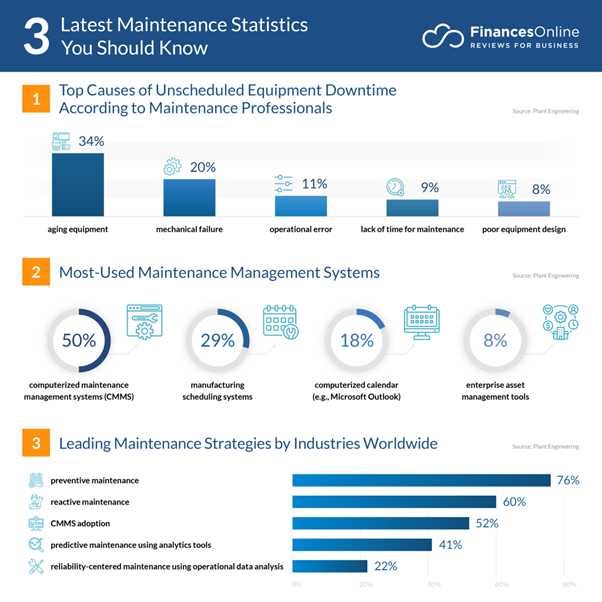
How to Implement a Preventive Maintenance Program
Implementing a preventive maintenance strategy requires a combination of planning, training, and ongoing analysis. With consistent monitoring and evaluation, organizations can develop, implement and optimize a successful preventive maintenance program that improves equipment reliability, reduces repair costs, and improves overall safety and compliance.
The implementation of a preventive maintenance program typically involves the following steps:
- Identify equipment and facilities that require maintenance: Review maintenance needs across the organization to determine the assets that are most critical to your operations. This may include machinery, vehicles, buildings, and other assets.
- Develop a schedule: Create a schedule for maintenance activities to guarantee that the tasks are performed at ideal intervals, preventing equipment failure and other issues. This may include a detailed SOP of the equipment, specific tasks and the recommended frequency.
- Train employees: Provide employees with the necessary tools and equipment to perform and complete maintenance tasks. Training employees on the proper procedures is vital to the success and effectiveness of the preventive maintenance program.
- Perform regular inspections: Conduct regular inspections and perform any necessary repairs to identify and prevent equipment failure or other issues. Once the preventive maintenance program has been implemented, these consistent assessments can ensure that equipment is always operating efficiently and reduce chances of long-term costly repairs.
- Monitor and evaluate the program: To make sure this preemptive maintenance approach is successful; it is crucial to monitor and evaluate its performance. This involves tracking key metrics, like equipment downtime and repair costs then adjusting the program to improve its effectiveness.
How an EAM or CMMS Can Help
A CMMS, or computerized maintenance management system, is a software tool that is used to manage maintenance activities, including preventive maintenance. It is designed to help organizations plan, schedule, and track maintenance and related tasks.
One of the primary ways a CMMS supports preventive maintenance is by providing a centralized database for storing and organizing historical and current maintenance information. An EAM/CMMS can assist organizations in developing a preventive maintenance schedule and automate it based on the information that is entered and stored in the system.
Once implemented, an EAM/CMMS can help organizations track and monitor the progress of their predictive maintenance activities. It can provide alerts and reminders to help ensure that maintenance tasks are performed on time and run reports to help organizations optimize their program.
If you are looking to improve your organization's preventive maintenance program, an EAM or CMMS solution can help. With the right tool, you can streamline your maintenance activities, reduce downtime, and improve the overall efficiency of your operations.
Schedule a demo to learn more about WebTMA and our product suite. Let’s level up your preventive maintenance program and drive results for your entire organization.
Ready for a Demo?
Interested in taking this to the next level? Sign up for a free demo with a TMA Systems Account Executive. Enter your email below and we will reserve a time for you to test drive WebTMA.
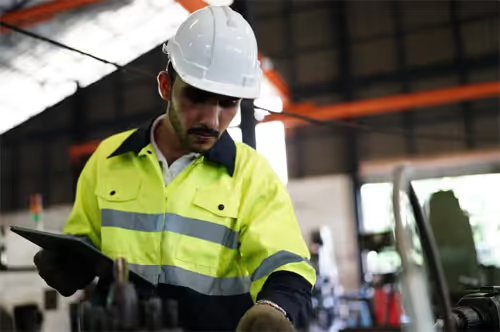
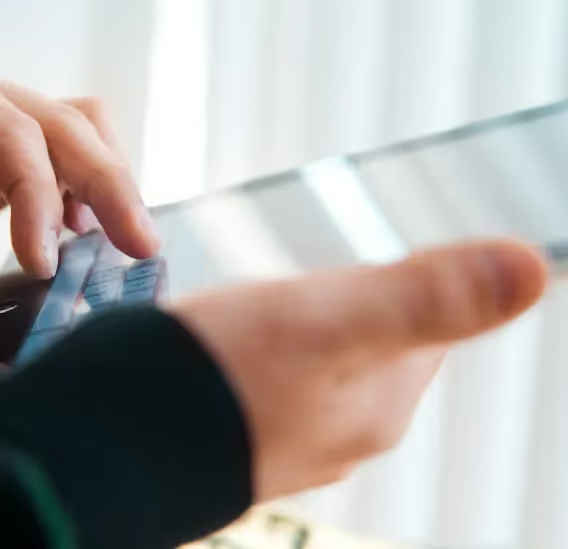
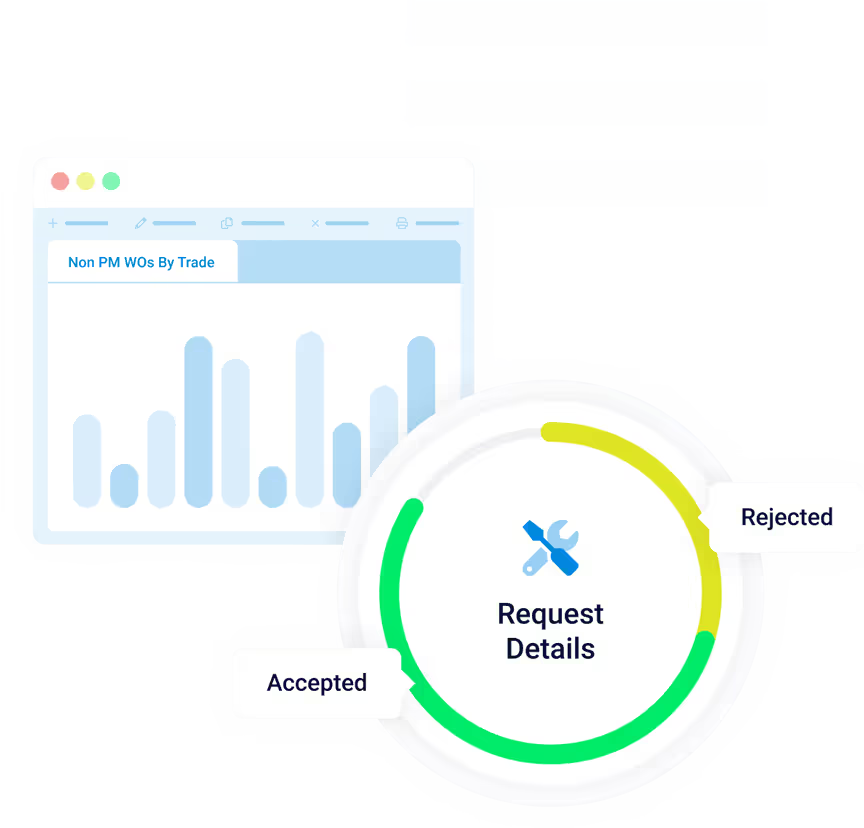