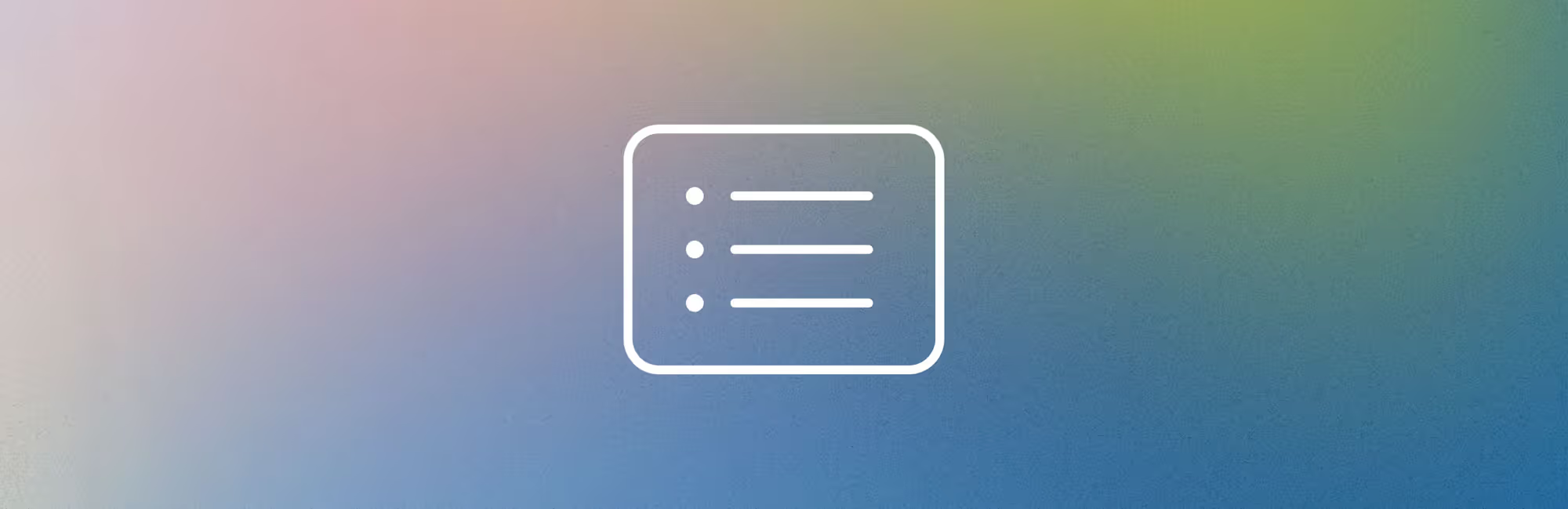
Efficient maintenance management is critical to the success of any organization that relies on equipment, vehicles, or facilities to operate effectively. Work orders are an essential tool that help keep track of maintenance requests, prioritize tasks, and reduce downtime. In this guide, we share best practices for creating, tracking, and completing work orders efficiently.
Why Work Orders Matter
Work orders help to improve organizations’ overall operational effectiveness, saving on time and resources, while increasing efficiency. They also ensure that all tasks are completed in accordance with safety and quality standards.
Types of Maintenance and Components
Maintenance work varies depending on its purpose. Common types of and approaches to maintenance include preventive maintenance, corrective maintenance, and reactive maintenance.
- Preventive maintenance tasks include regularly scheduled inspections, repairs, and replacements of components or systems to prevent breakdowns and reduce downtime.
- Corrective maintenance tasks are completed to fix existing problems with components or systems.
- Reactive maintenance tasks are completed after a system has malfunctioned or broken down. Components associated with maintenance work orders can include equipment, tools, and materials needed to complete the task.
Benefits of Efficient Work Orders
A typical work order includes key information, including location, description, urgency level, completion deadline, and materials required. These components allow you to prioritize tasks and allocate resources based on their importance and deadlines.
By streamlining your maintenance management with accurate and efficient work orders, you can reap several benefits:
- Increased productivity: Work orders provide clear instructions for technicians, reducing the time and effort required to complete tasks.
- Reduced downtime: With the documentation of prior tasks and by promptly addressing issues , organizations can reduce downtime and improve operational efficiency.
- Better resource allocation: Tracking work helps organizations properly allocate resources which ensures that the right personnel and materials are available when needed.
- Improved safety: Document the completion of maintenance tasksto certify that all work is completed in accordance with safety and quality standards.
- Cost savings: Organizations can make smarter decisions about future maintenance projects by tracking the cost of maintenance workwhich results in reduced overall maintenance costs.
Using CMMS to Streamline Processes
Computerized maintenance management software (CMMS) can help to streamline your work order process. CMMS provides a centralized system that enables a team to create, track, and complete work orders efficiently. With CMMS, you can easily report on and track the many variables of maintenance work, including cost, labor and overall ROI. Leveraging historical data and reports gives you the power to make smarter decisions about future projects.
Tips for Efficient Work Orders
Timely and systematic maintenance management is essential for any organization that relies on equipment, vehicles, or facilities to operate at its highest level. Work orders provide a clear roadmap of maintenance tasks.
This work order archive allows you to quickly identify potential problems, prioritize tasks, and allocate resources to complete them. By implementing a work order system, organizations can increase efficiency, save time and resources, and improve overall operational effectiveness.
Here are some tips for creating and completing work orders expertly:
- Standardize your format: Monitor advancement by implementing a standard system employing uniformity in the design and process of all tasks.
- Use clear and concise language: Avoid confusing technical jargon and acronyms by using simple language that technicians can understand.
- Prioritize tasks: Assign urgency levels to various assets like critical assets and prioritize tasks based on their importance and deadlines.
- Automate your work order process: Streamline the creation, tracking, and reporting of work orders by using computerized maintenance management software (CMMS).
- Regularly review and improve your process: Request regular feedback from employees or customers to improve your maintenance management process.
- Train your employees: Ensure everyone is aligned and correctly making use of the tools by training your employees on how to use the maintenance management system effectively.
- Communicate clearly: Communicate clearly with technicians and employees about service requests making sure everyone is aware of their responsibilities and deadlines.
- Track and analyze data: Use data from work completed and outstanding work orders to track trends and identify areas for improvement.
At TMA Systems, we offer a comprehensive CMMS that can help you streamline your maintenance management program. Contact us today to learn more about our solutions and how we can help you transform your facility maintenance operations.
Ready for a Demo?
Interested in taking this to the next level? Sign up for a free demo with a TMA Systems Account Executive. Enter your email below and we will reserve a time for you to test drive WebTMA.
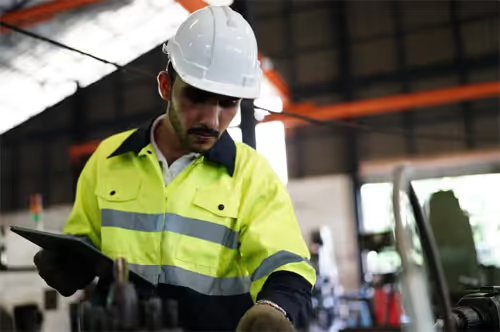
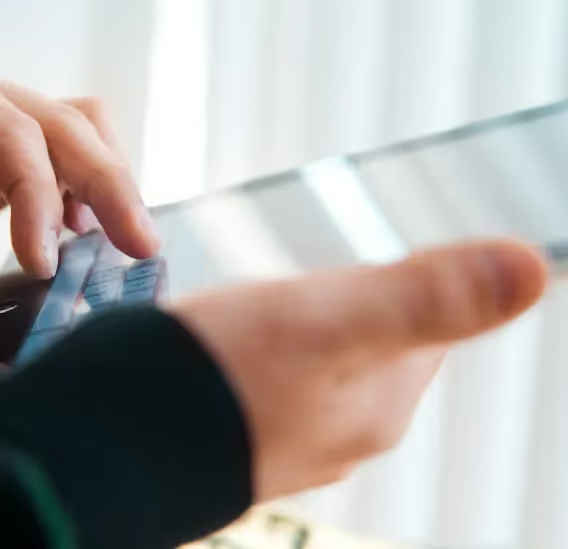
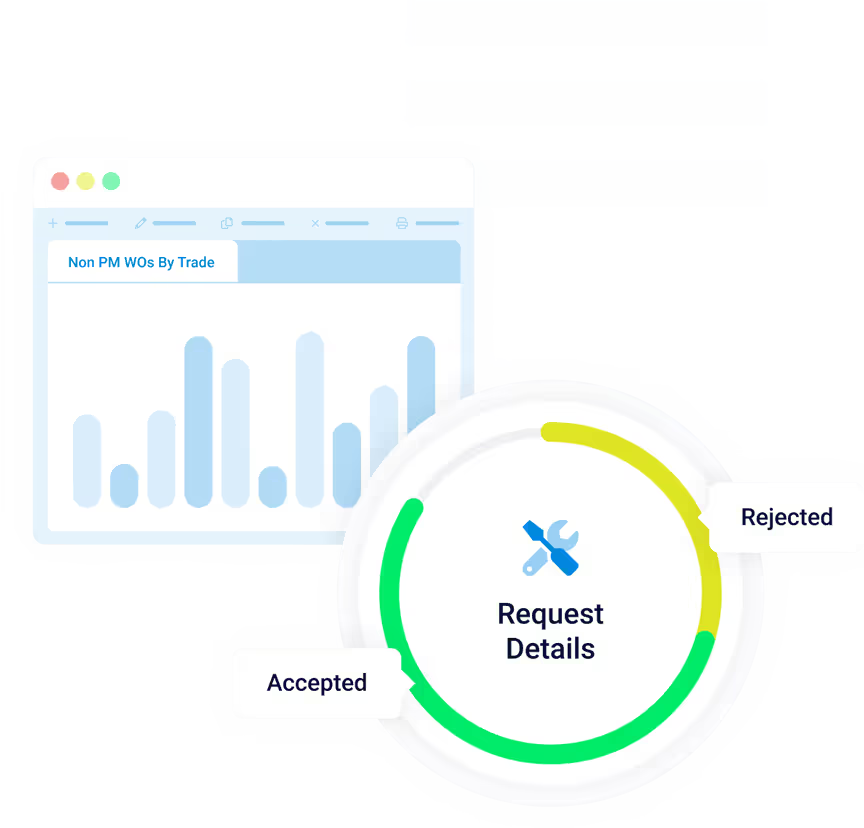