7 Tips for Effective Spare Parts Management
7 Tips for Effective Spare Parts Management
In this post
%20(1).avif)
1
2
3
7 Tips for Effective Spare Parts Management
Effective spare parts management helps reduce costs, boost efficiency, and prevent downtime by prioritizing critical spares, automating reorders, and leveraging CMMS/EAM tools. With actionable strategies, facilities teams can achieve tangible improvements in operations and sustainability.
Spare parts management is a critical component of asset reliability and maintenance efficiency. Poor management can lead to operational delays, higher costs, and unnecessary downtime. By integrating a Computerized Maintenance Management System (CMMS) or Enterprise Asset Management (EAM) solution into your strategy, you can streamline spare parts management and improve overall maintenance processes.
Here are seven actionable tips to optimize your spare parts management:
1. Conduct a Comprehensive Inventory Audit
The foundation for better decision-making and inventory control.
Conduct a thorough audit of your spare parts inventory. Identify the parts you currently have, their conditions, and their locations. A CMMS/EAM system simplifies this process by tracking inventory in real time, ensuring data accuracy about parts availability. This eliminates redundancy and ensures you have what you need when you need it.
2. Prioritize Critical Spares
Not all spare parts are of equal importance.
Classify parts based on their criticality to operations. Determine which items are high-priority (essential for core assets) and stock them in sufficient quantities. Less critical parts can be ordered on demand. CMMS/EAM solutions enable tagging and categorization of spare parts, making it easier to manage inventory by priority levels.
3. Automate Reorder Triggers
Maintain optimal inventory levels without manual tracking.
Out of stock parts can cause unexpected delays and operational losses. Use your CMMS/EAM system to set reorder points and minimum stock levels for key items. Automating these triggers ensures that inventory is replenished before it runs out, reducing risks of downtime and eliminating manual monitoring.
4. Integrate Maintenance and Inventory Systems
Seamlessly link inventory and maintenance management.
The integration of maintenance and inventory management with a CMMS/EAM elevates your operations. When maintenance teams create work orders, the system automatically links required parts from the inventory. This integration ensures seamless communication between maintenance and procurement departments and helps to avoid duplicate purchases.
5. Optimize Storage and Accessibility
Properly organize and label storage areas for easy access.
Efficient storage layouts and labeling systems minimize retrieval times and reduce errors. Using a CMMS/EAM, you can map storage locations and implement barcode scanning for quick identification of parts. This not saves time during maintenance and reduces the chance of misplaced inventory.
6. Focus on Supplier Management
Track supplier performance for dependability and efficiency.
Establishing strong relationships with reliable suppliers is a key aspect of spare parts management. CMMS/EAM platforms can track supplier performance, lead times, and costs, enabling you to make informed decisions about your supply chain. Diversifying suppliers for critical parts can also mitigate risks associated with delays or shortages from a single source.
7. Leverage Data for Predictive Insights
Identify trends and anticipate future needs.
CMMS/EAM solutions generate valuable data on spare parts usage, failure rates, and inventory turnover. Use these insights to identify patterns and trends. Investigate the root cause of frequently failing parts or stock more of it to minimize equipment downtime. Predictive analytics helps optimize inventory levels and improves overall equipment reliability.
By adopting WebTMA as your maintenance management solution, you can transform your spare parts management strategy. WebTMA helps reduce unnecessary inventory costs by preventing overstocking and stockouts, streamlines maintenance processes with real-time inventory visibility, and extends the lifespan of your assets through better planning and resource allocation. With its robust features and user-friendly interface, WebTMA is the ultimate tool for achieving excellence in spare parts management for all of your critical assets.
- Minimize downtime by making sure the right parts are always on hand
- Prevent overstocking and save money with smarter inventory tracking
- Keep operations running smoothly with better organization, visibility, and control.
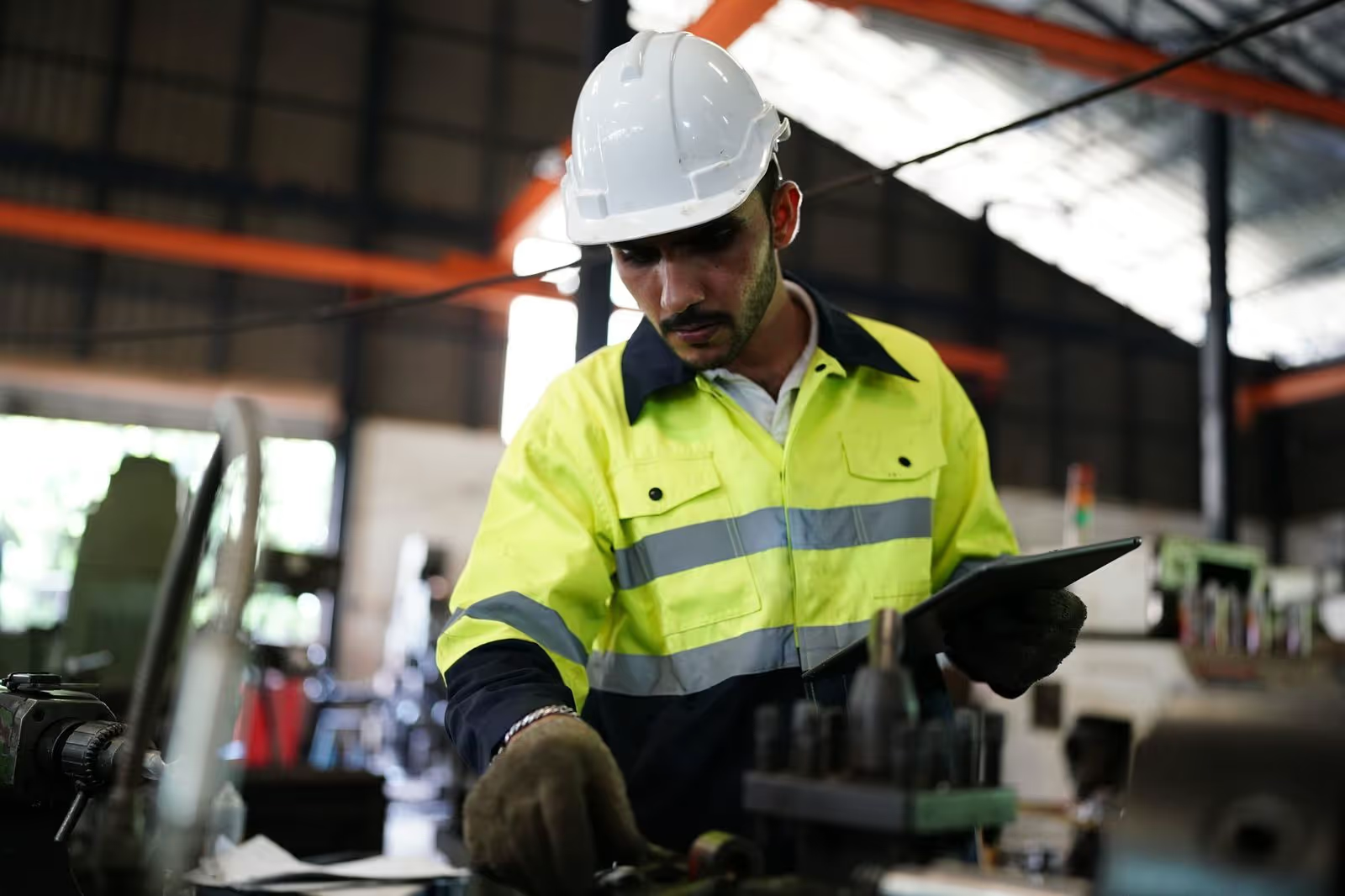
Download the eBook now
You’re all set!
Your eBook is on its way to your inbox. We hope it brings fresh insights and practical takeaways to help you get more from your maintenance operations.
Explore related resources
.avif)
7 Tips for Effective Spare Parts Management
Spare parts management is a critical component of asset reliability and maintenance efficiency. Poor management can lead to operational delays, higher costs, and unnecessary downtime. By integrating a Computerized Maintenance Management System (CMMS) or Enterprise Asset Management (EAM) solution into your strategy, you can streamline spare parts management and improve overall maintenance processes.
Here are seven actionable tips to optimize your spare parts management:
1. Conduct a Comprehensive Inventory Audit
The foundation for better decision-making and inventory control.
Conduct a thorough audit of your spare parts inventory. Identify the parts you currently have, their conditions, and their locations. A CMMS/EAM system simplifies this process by tracking inventory in real time, ensuring data accuracy about parts availability. This eliminates redundancy and ensures you have what you need when you need it.
2. Prioritize Critical Spares
Not all spare parts are of equal importance.
Classify parts based on their criticality to operations. Determine which items are high-priority (essential for core assets) and stock them in sufficient quantities. Less critical parts can be ordered on demand. CMMS/EAM solutions enable tagging and categorization of spare parts, making it easier to manage inventory by priority levels.
3. Automate Reorder Triggers
Maintain optimal inventory levels without manual tracking.
Out of stock parts can cause unexpected delays and operational losses. Use your CMMS/EAM system to set reorder points and minimum stock levels for key items. Automating these triggers ensures that inventory is replenished before it runs out, reducing risks of downtime and eliminating manual monitoring.
4. Integrate Maintenance and Inventory Systems
Seamlessly link inventory and maintenance management.
The integration of maintenance and inventory management with a CMMS/EAM elevates your operations. When maintenance teams create work orders, the system automatically links required parts from the inventory. This integration ensures seamless communication between maintenance and procurement departments and helps to avoid duplicate purchases.
5. Optimize Storage and Accessibility
Properly organize and label storage areas for easy access.
Efficient storage layouts and labeling systems minimize retrieval times and reduce errors. Using a CMMS/EAM, you can map storage locations and implement barcode scanning for quick identification of parts. This not saves time during maintenance and reduces the chance of misplaced inventory.
6. Focus on Supplier Management
Track supplier performance for dependability and efficiency.
Establishing strong relationships with reliable suppliers is a key aspect of spare parts management. CMMS/EAM platforms can track supplier performance, lead times, and costs, enabling you to make informed decisions about your supply chain. Diversifying suppliers for critical parts can also mitigate risks associated with delays or shortages from a single source.
7. Leverage Data for Predictive Insights
Identify trends and anticipate future needs.
CMMS/EAM solutions generate valuable data on spare parts usage, failure rates, and inventory turnover. Use these insights to identify patterns and trends. Investigate the root cause of frequently failing parts or stock more of it to minimize equipment downtime. Predictive analytics helps optimize inventory levels and improves overall equipment reliability.
By adopting WebTMA as your maintenance management solution, you can transform your spare parts management strategy. WebTMA helps reduce unnecessary inventory costs by preventing overstocking and stockouts, streamlines maintenance processes with real-time inventory visibility, and extends the lifespan of your assets through better planning and resource allocation. With its robust features and user-friendly interface, WebTMA is the ultimate tool for achieving excellence in spare parts management for all of your critical assets.
You’ve seen what’s possible—connect with us to learn how TMA Systems can support your goals beyond the event.
You’ve read the insights, now see how TMA Systems helps teams put them into practice.
From ideas to impact
You’ve read the insights, now see how TMA Systems helps teams put them into practice.
From screen to solution
You’ve watched what’s possible, now see how TMA Systems works for your organization.
From insight to implementation
You’ve explored the strategies, now see how we can bring them to life across your real facilities.