Minimizing equipment failure with effective lubrication maintenance
Minimizing equipment failure with effective lubrication maintenance
In this post
%20(1).avif)
Minimizing equipment failure with effective lubrication maintenance
Machine lubrication is a preventive maintenance technique of applying a lubricant, which is a type of oil in most cases, to equipment and its constituent parts.
Everyone understands the importance of keeping business-critical equipment optimally functioning. However, not all maintenance technicians and managers have the same level of clarity about what’s critical for preserving machine health. There are numerous factors, one of which is lubrication.
A comprehensive study by MIT revealed that 70% of machine failures can be attributed to surface degradation. The same study also determined that 79% of surface degradation is a result of mechanical wear that can be reduced by proper lubrication.
Understanding Machine Lubrication
Machine lubrication is a preventive maintenance technique of applying a lubricant, which is a type of oil in most cases, to equipment and its constituent parts. Through timely lubrication of equipment, maintenance managers can achieve a lot more than just reducing friction. When done as recommended, machine lubrication can:
To understand the significance of lubrication, one needs to be fully aware of the impact of friction on equipment. When two components move, rotate, or rub against each other, the friction between their surfaces generates heat – friction converts kinetic energy into thermal energy. The friction-induced thermal reaction is not ideal for hardware. Since most industrial machines operate for a greater part of the day, they generate a high level of heat due to friction. Lubrication reduces the friction between machine parts, which subsequently lessens the heat production. It also has the added benefit of making the machine operate smoother and with less noise.
Benefits of Lubrication in Maintenance
Lubrication is vital for the longevity of industrial machines rather than a menial chore that OEMs recommend. Here’s why:
Prevents premature component failure: Lubrication prevents machine parts from wearing out quickly, allowing you to leverage your industrial assets for their full, expected life span.
Reduces operational downtime due to unplanned equipment maintenance: Timely lubrication improves component performance and reduces the frequency of hardware replacements.
Prevents equipment damage due to overheating: Lubrication reduces friction, there by minimizing heat and keeping your assets at a sound operating temperature.
Reduces component wear and tear: Lubrication averts unexpected element wear and tear by ensuring the smooth functioning of hardware,
Decreases the impact of vibrations: Lubrication absorbs shocks and the effects of vibration, increasing safety and protecting both machines and their human operators.
Reduces corrosion: Lubrication safeguards metal components from rust by forming a protective layer, ensuring adequate insulation from environmental factors.
Protects from contaminants or debris: Lubrication draws contaminants away from components in motion preventing the surface erosion generated debris from affecting the function of the machinery.
Managing Lubrication with CMMS
Lubrication of industrial machinery is complex and requires expertise and experience. In order to eliminate the potential of human error, using a CMMS can help maintenance managers handle data related to preventive maintenance and lubrication programs. CMMS plays a role in:
Asset tracking: CMMS helps enterprises identify equipment that needs lubrication maintaining an in-depth database of lubricant specifications, equipment, and lubrication schedules.
Work orders and scheduling: CMMS creates work orders for lubrication tasks, including details on the required lubricants, the frequency of application, and the quantity to be used.
Inventory management: CMMS helps in ensuring the availability of sufficient lubricant when required through automated alerts for inventory levels and simplified reordering processes.
Data analysis and reporting: With CMMS, enterprises can analyze data related to lubrication tasks, including equipment reliability, lubricant performance, and usage trends. It can also generate reports that help in the identification of potential issues, optimization of lubrication schedules, and improvement of all-round equipment performance.
Employee training and certification: CMMS enables businesses to maintain employee certification and training records ensuring that the resources entrusted with lubrication tasks are equipped with the knowledge and skillset necessary to perform their duties effectively.
Optimizing Preventive Maintenance Scheduling with TMA Systems
Lubrication maintenance brings exponential benefits to enterprises in the form of reduced operational downtime, disruptions, and expenses. Complementing human capability with software-driven precision, a trusted CMMS provider like TMA Systems can help to manage all preventive maintenance scheduling tasks.
TMA Systems is a leading technology partner, dedicated to delivering reliable, innovative, and trusted facility maintenance management solutions. We not only provide cutting-edge tools to automate and streamline industrial functions like lubrication but also conduct audits to identify areas for improvement and address mission-critical concerns. Our teams also offer in-depth training and support to ensure that your maintenance staff can utilize and manage maintenance data with ease.
More than 1,650 organizations across industries trust our products. So, you can expect a comprehensive, world-class enterprise asset management solution at your disposal to maximize OEE, ROI, and asset life span.
To learn more about how your company can benefit from our CMMS solutions and optimize your PM programs, schedule a demo today.
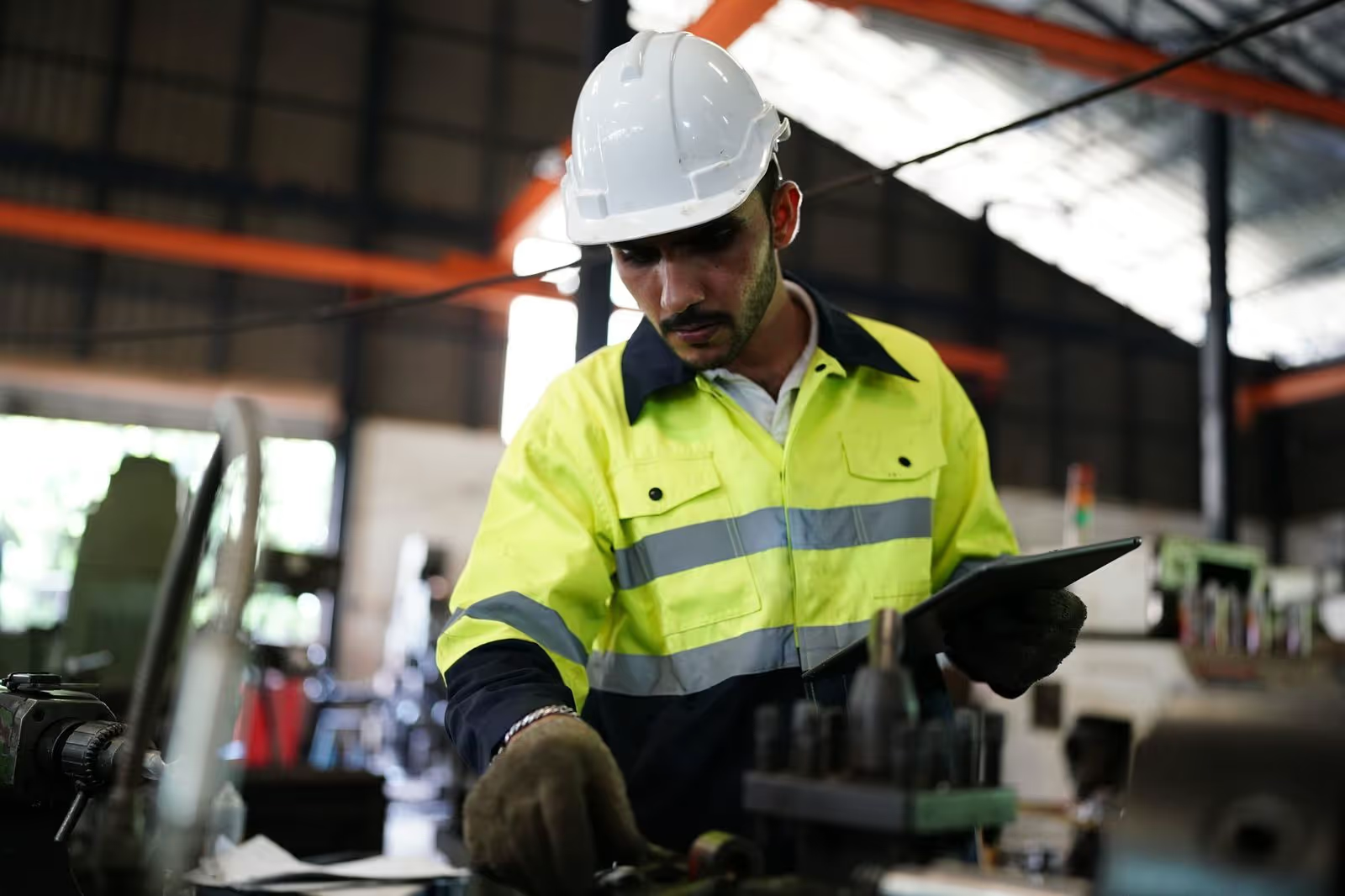
Download the eBook now
You’re all set!
Your eBook is on its way to your inbox. We hope it brings fresh insights and practical takeaways to help you get more from your maintenance operations.
Explore related resources
.avif)
Minimizing equipment failure with effective lubrication maintenance
Everyone understands the importance of keeping business-critical equipment optimally functioning. However, not all maintenance technicians and managers have the same level of clarity about what’s critical for preserving machine health. There are numerous factors, one of which is lubrication.
A comprehensive study by MIT revealed that 70% of machine failures can be attributed to surface degradation. The same study also determined that 79% of surface degradation is a result of mechanical wear that can be reduced by proper lubrication.
Understanding Machine Lubrication
Machine lubrication is a preventive maintenance technique of applying a lubricant, which is a type of oil in most cases, to equipment and its constituent parts. Through timely lubrication of equipment, maintenance managers can achieve a lot more than just reducing friction. When done as recommended, machine lubrication can:
To understand the significance of lubrication, one needs to be fully aware of the impact of friction on equipment. When two components move, rotate, or rub against each other, the friction between their surfaces generates heat – friction converts kinetic energy into thermal energy. The friction-induced thermal reaction is not ideal for hardware. Since most industrial machines operate for a greater part of the day, they generate a high level of heat due to friction. Lubrication reduces the friction between machine parts, which subsequently lessens the heat production. It also has the added benefit of making the machine operate smoother and with less noise.
Benefits of Lubrication in Maintenance
Lubrication is vital for the longevity of industrial machines rather than a menial chore that OEMs recommend. Here’s why:
Prevents premature component failure: Lubrication prevents machine parts from wearing out quickly, allowing you to leverage your industrial assets for their full, expected life span.
Reduces operational downtime due to unplanned equipment maintenance: Timely lubrication improves component performance and reduces the frequency of hardware replacements.
Prevents equipment damage due to overheating: Lubrication reduces friction, there by minimizing heat and keeping your assets at a sound operating temperature.
Reduces component wear and tear: Lubrication averts unexpected element wear and tear by ensuring the smooth functioning of hardware,
Decreases the impact of vibrations: Lubrication absorbs shocks and the effects of vibration, increasing safety and protecting both machines and their human operators.
Reduces corrosion: Lubrication safeguards metal components from rust by forming a protective layer, ensuring adequate insulation from environmental factors.
Protects from contaminants or debris: Lubrication draws contaminants away from components in motion preventing the surface erosion generated debris from affecting the function of the machinery.
Managing Lubrication with CMMS
Lubrication of industrial machinery is complex and requires expertise and experience. In order to eliminate the potential of human error, using a CMMS can help maintenance managers handle data related to preventive maintenance and lubrication programs. CMMS plays a role in:
Asset tracking: CMMS helps enterprises identify equipment that needs lubrication maintaining an in-depth database of lubricant specifications, equipment, and lubrication schedules.
Work orders and scheduling: CMMS creates work orders for lubrication tasks, including details on the required lubricants, the frequency of application, and the quantity to be used.
Inventory management: CMMS helps in ensuring the availability of sufficient lubricant when required through automated alerts for inventory levels and simplified reordering processes.
Data analysis and reporting: With CMMS, enterprises can analyze data related to lubrication tasks, including equipment reliability, lubricant performance, and usage trends. It can also generate reports that help in the identification of potential issues, optimization of lubrication schedules, and improvement of all-round equipment performance.
Employee training and certification: CMMS enables businesses to maintain employee certification and training records ensuring that the resources entrusted with lubrication tasks are equipped with the knowledge and skillset necessary to perform their duties effectively.
Optimizing Preventive Maintenance Scheduling with TMA Systems
Lubrication maintenance brings exponential benefits to enterprises in the form of reduced operational downtime, disruptions, and expenses. Complementing human capability with software-driven precision, a trusted CMMS provider like TMA Systems can help to manage all preventive maintenance scheduling tasks.
TMA Systems is a leading technology partner, dedicated to delivering reliable, innovative, and trusted facility maintenance management solutions. We not only provide cutting-edge tools to automate and streamline industrial functions like lubrication but also conduct audits to identify areas for improvement and address mission-critical concerns. Our teams also offer in-depth training and support to ensure that your maintenance staff can utilize and manage maintenance data with ease.
More than 1,650 organizations across industries trust our products. So, you can expect a comprehensive, world-class enterprise asset management solution at your disposal to maximize OEE, ROI, and asset life span.
To learn more about how your company can benefit from our CMMS solutions and optimize your PM programs, schedule a demo today.
You’ve seen what’s possible—connect with us to learn how TMA Systems can support your goals beyond the event.
You’ve read the insights, now see how TMA Systems helps teams put them into practice.
From ideas to impact
You’ve read the insights, now see how TMA Systems helps teams put them into practice.
From screen to solution
You’ve watched what’s possible, now see how TMA Systems works for your organization.
From insight to implementation
You’ve explored the strategies, now see how we can bring them to life across your real facilities.