CMMS Preventive Maintenance Tips & Checklist
CMMS Preventive Maintenance Tips & Checklist
In this post
%20(1).avif)
CMMS Preventive Maintenance Tips & Checklist
Our blog provides tips on how to use CMMS Preventive Maintenance. Get smart advice from TMA Systems and keep your equipment running smoothly
CMMS Preventive Maintenance Tips & Checklist
For most companies, maintenance represents a very significant function within the overall production environment. Automation has undergone substantial developments over the past years. The resulting complexity of the systems has made the reliability and good functionality of the machines more important than ever. This is especially true in the process industry, characterized by expensive specialized equipment and stringent environmental considerations. With profit margins decreasing, the need for a good maintenance planning and control system like CMMS is obvious for Preventive Maintenance.
Most of the time, a good preventive maintenance plan is the result of many combined efforts and not just one single silver bullet. With increased mechanization and automation, consistent maintenance is paramount. Repair and replacement costs are oftentimes extremely high, and facility and manufacturing management managers can avoid them only through planning a systematized inspection. A skipped process can result in a machine breaking down, an occurrence that will dramatically impact productivity and will incur substantial expenses.
In addition to helping managers identify equipment that may require maintenance, preventive maintenance checklists also ensure that needed spare parts and materials are on hand in the event of a machine breaking down. At the same time, maintenance checklists allow maintenance professionals to document work they have done on the facility and machinery. In case anything goes wrong and a piece of equipment fails, maintenance checklists come very handy as proof of having performed your due diligence.
Creating a Maintenance Checklist for Your Facility
The first step that goes into proper preventive maintenance is creating individual checklists for each of the facilities you manage. A one-size-fits-all checklist is not recommended if you are in charge of several facilities because they often have different assets and buildings. Create a checklist for every building in your facility. Start from the top of the building, writing down each part that requires maintenance and breaking the process into several actionable steps. Include a checkbox alongside each step of each maintenance process, as well as a blank space for the employee to write the date when maintenance was performed.
4 Steps to World-Class Manufacturing Maintenance
Given the complexity of the maintenance process, there are several steps you need to take in order to achieve an efficient maintenance plan for your facility. We have broken down this process into 4 essential steps:
1. Gather Data and Calculate Downtime Costs
Gather data about machine downtime, technology usage, meantime between machine failures, expenditures on parts, technician response time, and an estimative percentage of on-time deliveries. This is the very first and most important step you need to take before transitioning to manufacturing maintenance best practices.
2. Determine the Value of Maintenance
After calculating the average per-hour downtime cost, you can estimate how much money maintenance improvements can save. Reasonable assumptions can be made by applying the per-hour cost to machine availability in order to determine how much value an increase in availability can add to the organization. Sometimes, even a small increase of 5 percent translates into a significant improvement.
3. Identify Maintenance Tasks
After assessing the potential savings of consistent maintenance, the next step is identifying maintenance tasks. Reliability-centered maintenance is the most effective methodology to use, as it comprehensively analyzes operational variables, helping establish minimum levels of maintenance in your facility. This analysis will result in a list of tasks that will then be grouped into sensible categories on your preventive maintenance checklist. Sometimes, doing some smoothing and streamlining of these groups of tasks is necessary to achieve a good maintenance checklist.
4. Schedule Maintenance Tasks
The checklist you have created must be transformed into a long-range plan of forecasted maintenance work. Each task included on the checklist must be scheduled and completed adequately. Note that, while some tasks should be performed frequently (e.g. every month), others may be performed every 3 or even 6 months. It is important to establish appropriate time intervals for each task in order to ensure that your preventive maintenance plan is efficient and helps minimize downtime costs as well.
Building Maintenance Windows into Production Plans
Preventative maintenance can take time, from a few hours to days, depending on the complexity of the process. This can greatly impact products, as production units have to stop working and make the equipment available to the maintenance crew. In order to prevent a decrease in productivity, manufacturing maintenance managers should build maintenance windows into production plans.
For example, it could be agreed that on Wednesday morning Production Unit 1 will stop production and make the equipment available to the maintenance crew for, say, five hours. During this maintenance window, the maintenance crew can successfully assign as many people as required to complete the planned maintenance fast and get the equipment back to work until the following week.
Creating tables or checklists in which maintenance windows are built into production plans will not interfere with the general productivity of the facility. Usually, using a CMMS system provides a relatively easy solution to scheduling and planning preventative maintenance, helping reduce downtime costs to a great extent.
Call TMA Systems, Inc. to see how our customizable software can benefit you, call us at +1.918.858.6600 or email marketing@tmasystems.com
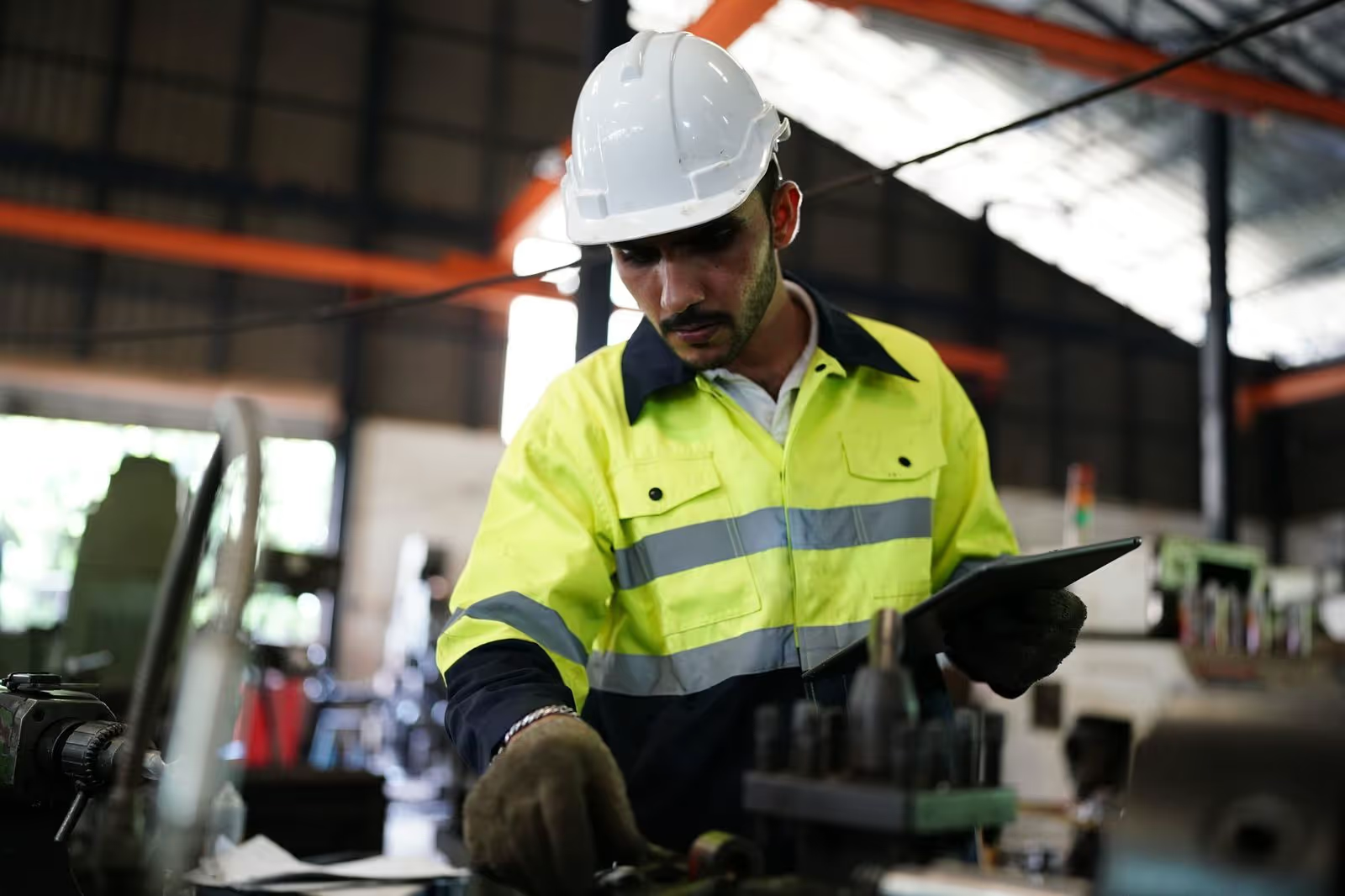
Download the eBook now
You’re all set!
Your eBook is on its way to your inbox. We hope it brings fresh insights and practical takeaways to help you get more from your maintenance operations.
Explore related resources
.avif)
CMMS Preventive Maintenance Tips & Checklist
CMMS Preventive Maintenance Tips & Checklist
For most companies, maintenance represents a very significant function within the overall production environment. Automation has undergone substantial developments over the past years. The resulting complexity of the systems has made the reliability and good functionality of the machines more important than ever. This is especially true in the process industry, characterized by expensive specialized equipment and stringent environmental considerations. With profit margins decreasing, the need for a good maintenance planning and control system like CMMS is obvious for Preventive Maintenance.
Most of the time, a good preventive maintenance plan is the result of many combined efforts and not just one single silver bullet. With increased mechanization and automation, consistent maintenance is paramount. Repair and replacement costs are oftentimes extremely high, and facility and manufacturing management managers can avoid them only through planning a systematized inspection. A skipped process can result in a machine breaking down, an occurrence that will dramatically impact productivity and will incur substantial expenses.
In addition to helping managers identify equipment that may require maintenance, preventive maintenance checklists also ensure that needed spare parts and materials are on hand in the event of a machine breaking down. At the same time, maintenance checklists allow maintenance professionals to document work they have done on the facility and machinery. In case anything goes wrong and a piece of equipment fails, maintenance checklists come very handy as proof of having performed your due diligence.
Creating a Maintenance Checklist for Your Facility
The first step that goes into proper preventive maintenance is creating individual checklists for each of the facilities you manage. A one-size-fits-all checklist is not recommended if you are in charge of several facilities because they often have different assets and buildings. Create a checklist for every building in your facility. Start from the top of the building, writing down each part that requires maintenance and breaking the process into several actionable steps. Include a checkbox alongside each step of each maintenance process, as well as a blank space for the employee to write the date when maintenance was performed.
4 Steps to World-Class Manufacturing Maintenance
Given the complexity of the maintenance process, there are several steps you need to take in order to achieve an efficient maintenance plan for your facility. We have broken down this process into 4 essential steps:
1. Gather Data and Calculate Downtime Costs
Gather data about machine downtime, technology usage, meantime between machine failures, expenditures on parts, technician response time, and an estimative percentage of on-time deliveries. This is the very first and most important step you need to take before transitioning to manufacturing maintenance best practices.
2. Determine the Value of Maintenance
After calculating the average per-hour downtime cost, you can estimate how much money maintenance improvements can save. Reasonable assumptions can be made by applying the per-hour cost to machine availability in order to determine how much value an increase in availability can add to the organization. Sometimes, even a small increase of 5 percent translates into a significant improvement.
3. Identify Maintenance Tasks
After assessing the potential savings of consistent maintenance, the next step is identifying maintenance tasks. Reliability-centered maintenance is the most effective methodology to use, as it comprehensively analyzes operational variables, helping establish minimum levels of maintenance in your facility. This analysis will result in a list of tasks that will then be grouped into sensible categories on your preventive maintenance checklist. Sometimes, doing some smoothing and streamlining of these groups of tasks is necessary to achieve a good maintenance checklist.
4. Schedule Maintenance Tasks
The checklist you have created must be transformed into a long-range plan of forecasted maintenance work. Each task included on the checklist must be scheduled and completed adequately. Note that, while some tasks should be performed frequently (e.g. every month), others may be performed every 3 or even 6 months. It is important to establish appropriate time intervals for each task in order to ensure that your preventive maintenance plan is efficient and helps minimize downtime costs as well.
Building Maintenance Windows into Production Plans
Preventative maintenance can take time, from a few hours to days, depending on the complexity of the process. This can greatly impact products, as production units have to stop working and make the equipment available to the maintenance crew. In order to prevent a decrease in productivity, manufacturing maintenance managers should build maintenance windows into production plans.
For example, it could be agreed that on Wednesday morning Production Unit 1 will stop production and make the equipment available to the maintenance crew for, say, five hours. During this maintenance window, the maintenance crew can successfully assign as many people as required to complete the planned maintenance fast and get the equipment back to work until the following week.
Creating tables or checklists in which maintenance windows are built into production plans will not interfere with the general productivity of the facility. Usually, using a CMMS system provides a relatively easy solution to scheduling and planning preventative maintenance, helping reduce downtime costs to a great extent.
Call TMA Systems, Inc. to see how our customizable software can benefit you, call us at +1.918.858.6600 or email marketing@tmasystems.com
You’ve seen what’s possible—connect with us to learn how TMA Systems can support your goals beyond the event.
You’ve read the insights, now see how TMA Systems helps teams put them into practice.
From ideas to impact
You’ve read the insights, now see how TMA Systems helps teams put them into practice.
From screen to solution
You’ve watched what’s possible, now see how TMA Systems works for your organization.
From insight to implementation
You’ve explored the strategies, now see how we can bring them to life across your real facilities.