Addressing Labor Shortage and Skill Deficits in Maintenance Management
Addressing Labor Shortage and Skill Deficits in Maintenance Management
In this post
%20(1).avif)
1
2
3
Addressing Labor Shortage and Skill Deficits in Maintenance Management
Many organizations are currently experiencing labor shortage and skill deficit in maintenance management, a situation that is hindering the effectiveness of organizations for sustainable operations.
As of July 2021, an average of 13.6 million jobs remained unfilled for a month across the US. It was a particularly surprising development, especially with such a high unemployment rate in 2020 due to COVID-19. Throughout 2021, people continued to resign from their jobs and many chose not to return to the workforce despite the global economic rebound from the disruptions and losses., A report by the U.S. Bureau of Labor Statistics summed up the situation perfectly – more than 4.3 million resignations were tendered in November 2021, taking the annual number of resignations across the US to a record 48 million.
While this labor shortage is plaguing all facets of businesses across industries, its impact is most acute on industrial maintenance and facilities management. At 47 years of age, an average general maintenance worker is at the cusp of leaving the workforce, creating a void that is difficult for enterprises to fill. The aging workforce deployed to maintenance functionalities is finding it difficult to adapt to the “new normal” while the ‘millennials’ – who will make up 75% of the global workforce by 2025 – are put off by conventional industrial maintenance methodologies. Digital transformation is paramount, but operational coherence and business continuity will rely heavily on a smooth transition of workforces and processes. It’s becoming clear that there is no one-stop solution to the labor shortage issue.
Acknowledging and Understanding the Skill Gap
Enterprise leaders must begin to accept that there is a talent crisis in industrial maintenance and facility management requiring immediate and holistic remediation. Meticulous planning, digital strategies, and efficient learning and development modules are key in addressing the concern. Enterprises must also revisit their operating models to align with the changing preferences of the millennial workforce.
Industrial maintenance and facility management demand a specific skillset garnered over time. This makes it exceedingly difficult to find like-for-like replacements for outgoing maintenance specialists. Similarly, it can be considerably difficult for enterprises to completely digitize their maintenance processes within weeks in order to fill the job roles which were once held by employees with requisite digital skills.
The three main reasons for this talent crisis:
- A mass exodus of the older generation: The aging maintenance workforce is making way for the millennials, but the transition is not seamless. As they leave with their maintenance-specific capabilities, production uptime and reliability are the two most significant areas of concern for enterprises.
- The reluctance of the new generation: In the digital age, the younger generation shows a lack of keenness to pursue industrial maintenance as their choice of career due in part to the looming possibility of large-scale automation. Additionally, other positions and functionalities within the workforces offer better monetary opportunities and flexibility.
- A deficit of purpose-specific talent in a digital paradigm: While industrial maintenance and facilities management will rely heavily on the doctrines of Industry 4.0, there is a skill gap among technicians – both old and new – around the maintenance and management of cyber-physical assets. A new-age, future-ready industrial maintenance technician must have the requisite knowledge to execute both physical and software-based tasks.
Bridging the Gaps, Addressing the Deficits
With the problems identified, enterprises must establish and meticulously execute. However, organizations rushing these changes will lead to an eventual failure to meet the objectives. Enterprises must thoroughly analyze the state of their maintenance management excellence and align the leadership, the maintenance management team, and human resources to resolve the talent deficit. The three most important considerations for them should be:
- Retaining the old, onboarding the new, striking the right balance: The key to a smooth transition is leveraging the capabilities of the old hands while bringing in the next generation into the system. The existing workforce possess the intrinsic knowledge of the industrial maintenance processes, which is vital for continuity. This knowledge can be passed on to new personnel with technology-inclined capabilities. Synergizing the capabilities of the old and the new, and dividing work orders and tasks based on specialization can be the swiftest way forward for industrial maintenance and facility management for forward-looking enterprises.
- Developing an outcome-oriented training program to align capabilities with objectives: A sure way of addressing skill deficits is to upskill and train the workforce. With intelligently developed and customized training modules, enterprises can align and empower the workforce in totality.
- Adopting technologies to unlock value at scale: The changed paradigm of business operations will heavily rely on technological innovations and holistic digital transformation. So, while there is a transition in workforce and a seamless handover of the maintenance baton, enterprises must strongly pursue their digital goals and automate maintenance management functionalities as swiftly as possible. Innovations in the fields of AI/ML, RPA, industrial IoT, cloud computing, predictive and prescriptive analytics, and AR/VR will shape the future of maintenance management, and the sooner enterprises can embark on the digital transformation, the better it is for them.
Strengthening Maintenance Management with Strategic Technology Partnerships
To digitize maintenance management in-house while also addressing the labor shortage can put too much pressure on enterprises. Forging a strategic partnership with technology experts who come with consolidated, end-to-end capabilities is a better alternative than taking it on alone. Enterprises can then focus on their core competencies while the technology partner adds the digital layers necessary to streamline industrial maintenance and facility management.
Two of the key elements of such a digitization are computerized maintenance management systems (CMMS) and enterprise asset management (EAM) systems. These systems enable seamless creation, communication, and monitoring of work schedules and empower maintenance technicians to better execute their jobs. The automated job scheduling through these systems allows enterprises to distribute work more efficiently and intuitively while largely resolving the issues caused by labor shortage and skill deficits.
It is time for enterprises to attach a greater significance to maintenance management and optimize resources and assets. Through intelligent training programs, adoption of new-age digital innovations, and synergizing capabilities, enterprises can address the talent crisis and emerge prepared for a future that promises abundant opportunities.
To read more about the impending labor shortage and how a strategic technology partner, like TMA Systems, can help enterprises overcome the challenge, download our whitepaper.
- Do more with fewer resources by automating routine tasks and streamlining workflows.
- Bridge the skills gap with intuitive tools that support faster training and onboarding.
- Retain top talent by reducing burnout and enabling teams to work more efficiently.
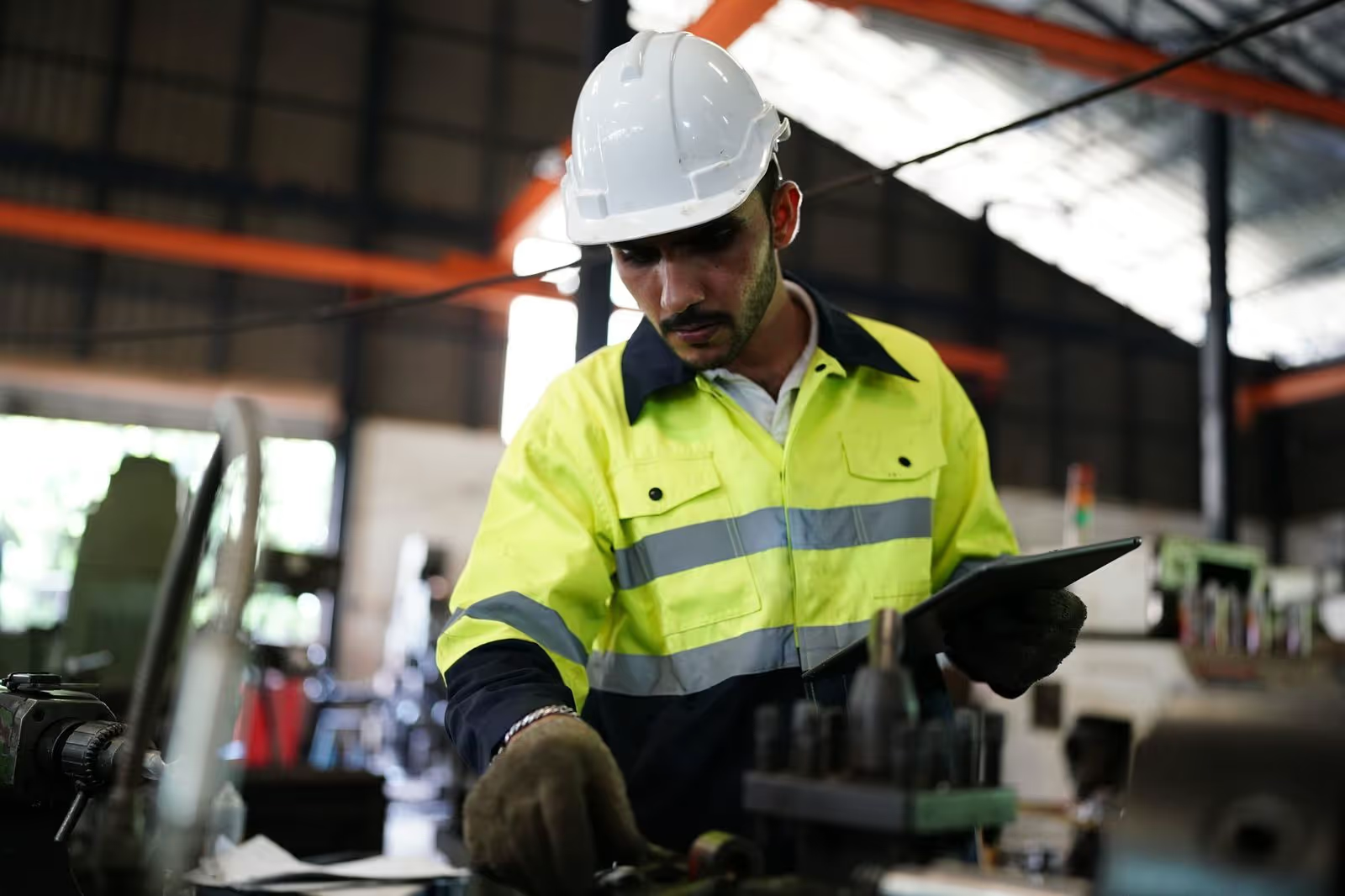
Download the eBook now
You’re all set!
Your eBook is on its way to your inbox. We hope it brings fresh insights and practical takeaways to help you get more from your maintenance operations.
Explore related resources
.avif)
Addressing Labor Shortage and Skill Deficits in Maintenance Management
As of July 2021, an average of 13.6 million jobs remained unfilled for a month across the US. It was a particularly surprising development, especially with such a high unemployment rate in 2020 due to COVID-19. Throughout 2021, people continued to resign from their jobs and many chose not to return to the workforce despite the global economic rebound from the disruptions and losses., A report by the U.S. Bureau of Labor Statistics summed up the situation perfectly – more than 4.3 million resignations were tendered in November 2021, taking the annual number of resignations across the US to a record 48 million.
While this labor shortage is plaguing all facets of businesses across industries, its impact is most acute on industrial maintenance and facilities management. At 47 years of age, an average general maintenance worker is at the cusp of leaving the workforce, creating a void that is difficult for enterprises to fill. The aging workforce deployed to maintenance functionalities is finding it difficult to adapt to the “new normal” while the ‘millennials’ – who will make up 75% of the global workforce by 2025 – are put off by conventional industrial maintenance methodologies. Digital transformation is paramount, but operational coherence and business continuity will rely heavily on a smooth transition of workforces and processes. It’s becoming clear that there is no one-stop solution to the labor shortage issue.
Acknowledging and Understanding the Skill Gap
Enterprise leaders must begin to accept that there is a talent crisis in industrial maintenance and facility management requiring immediate and holistic remediation. Meticulous planning, digital strategies, and efficient learning and development modules are key in addressing the concern. Enterprises must also revisit their operating models to align with the changing preferences of the millennial workforce.
Industrial maintenance and facility management demand a specific skillset garnered over time. This makes it exceedingly difficult to find like-for-like replacements for outgoing maintenance specialists. Similarly, it can be considerably difficult for enterprises to completely digitize their maintenance processes within weeks in order to fill the job roles which were once held by employees with requisite digital skills.
The three main reasons for this talent crisis:
- A mass exodus of the older generation: The aging maintenance workforce is making way for the millennials, but the transition is not seamless. As they leave with their maintenance-specific capabilities, production uptime and reliability are the two most significant areas of concern for enterprises.
- The reluctance of the new generation: In the digital age, the younger generation shows a lack of keenness to pursue industrial maintenance as their choice of career due in part to the looming possibility of large-scale automation. Additionally, other positions and functionalities within the workforces offer better monetary opportunities and flexibility.
- A deficit of purpose-specific talent in a digital paradigm: While industrial maintenance and facilities management will rely heavily on the doctrines of Industry 4.0, there is a skill gap among technicians – both old and new – around the maintenance and management of cyber-physical assets. A new-age, future-ready industrial maintenance technician must have the requisite knowledge to execute both physical and software-based tasks.
Bridging the Gaps, Addressing the Deficits
With the problems identified, enterprises must establish and meticulously execute. However, organizations rushing these changes will lead to an eventual failure to meet the objectives. Enterprises must thoroughly analyze the state of their maintenance management excellence and align the leadership, the maintenance management team, and human resources to resolve the talent deficit. The three most important considerations for them should be:
- Retaining the old, onboarding the new, striking the right balance: The key to a smooth transition is leveraging the capabilities of the old hands while bringing in the next generation into the system. The existing workforce possess the intrinsic knowledge of the industrial maintenance processes, which is vital for continuity. This knowledge can be passed on to new personnel with technology-inclined capabilities. Synergizing the capabilities of the old and the new, and dividing work orders and tasks based on specialization can be the swiftest way forward for industrial maintenance and facility management for forward-looking enterprises.
- Developing an outcome-oriented training program to align capabilities with objectives: A sure way of addressing skill deficits is to upskill and train the workforce. With intelligently developed and customized training modules, enterprises can align and empower the workforce in totality.
- Adopting technologies to unlock value at scale: The changed paradigm of business operations will heavily rely on technological innovations and holistic digital transformation. So, while there is a transition in workforce and a seamless handover of the maintenance baton, enterprises must strongly pursue their digital goals and automate maintenance management functionalities as swiftly as possible. Innovations in the fields of AI/ML, RPA, industrial IoT, cloud computing, predictive and prescriptive analytics, and AR/VR will shape the future of maintenance management, and the sooner enterprises can embark on the digital transformation, the better it is for them.
Strengthening Maintenance Management with Strategic Technology Partnerships
To digitize maintenance management in-house while also addressing the labor shortage can put too much pressure on enterprises. Forging a strategic partnership with technology experts who come with consolidated, end-to-end capabilities is a better alternative than taking it on alone. Enterprises can then focus on their core competencies while the technology partner adds the digital layers necessary to streamline industrial maintenance and facility management.
Two of the key elements of such a digitization are computerized maintenance management systems (CMMS) and enterprise asset management (EAM) systems. These systems enable seamless creation, communication, and monitoring of work schedules and empower maintenance technicians to better execute their jobs. The automated job scheduling through these systems allows enterprises to distribute work more efficiently and intuitively while largely resolving the issues caused by labor shortage and skill deficits.
It is time for enterprises to attach a greater significance to maintenance management and optimize resources and assets. Through intelligent training programs, adoption of new-age digital innovations, and synergizing capabilities, enterprises can address the talent crisis and emerge prepared for a future that promises abundant opportunities.
To read more about the impending labor shortage and how a strategic technology partner, like TMA Systems, can help enterprises overcome the challenge, download our whitepaper.
You’ve seen what’s possible—connect with us to learn how TMA Systems can support your goals beyond the event.
You’ve read the insights, now see how TMA Systems helps teams put them into practice.
From ideas to impact
You’ve read the insights, now see how TMA Systems helps teams put them into practice.
From screen to solution
You’ve watched what’s possible, now see how TMA Systems works for your organization.
From insight to implementation
You’ve explored the strategies, now see how we can bring them to life across your real facilities.