Request a live demo to see how WebTMA helps streamline maintenance, boost asset performance, and simplify complex workflows.
Our team will tailor the walkthrough to your operations, highlighting the features that solve your day-to-day challenges and support your long-term goals.
"It's not just the salesperson that wants to see you succeed; they all do. Many have worked with me on a 1:1 to walk through the steps with me to identify the problem, test it, and help me resolve it."
"What has impressed me the most with TMA is their listening ear in allowing the customer to drive software updates and enhancements."
"Customer support for the product has been excellent over the years. The support team is often able to help resolve the issue in the initial contact."
"Our company’s experience with TMA has been stellar. I’ve been involved with other CMMS programs, the user interface is much easier with TMA and the customer support is second to none.”
“In this day and age, we are constantly being forced to do more with less and the software enables us to manage and handle a greater number of work requests and problems within our organization with less people.”
“It’s got a permanent resonance. It provides exactly what we need. It’s part of our business practice. It’s baked in.”
“TMA has offered a great deal to the park. It has allowed us to move from a reactive maintenance approach to a proactive maintenance approach giving us more data on maintenance costs and parts usage.”
Comprehensive facility management platform for enterprise
From multi-site tracking to team coordination and compliance, WebTMA is enterprise asset management software that keeps operations moving and makes maintenance management a strategic advantage.
30+ optional modules
50+ built-in tools
Secure deployment
Scalable & integration-ready
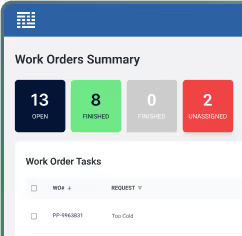
.avif)
From work orders to asset intelligence
Most CMMS software organizes, tracks, and optimizes maintenance across assets, teams, and sites. WebTMA goes further, combining enterprise scalability, automation, and asset intelligence in one configurable platform built for complex environments.
Reduce downtime
Minimize disruptions with proactive tools for planned, preventive, and predictive maintenance.
98% of WebTMA customers report decreases in unplanned downtime.
Improve communication
Give every team in your organization access to the same data. No silos, no crossed wires.
57% of customers reduce admin time significantly within the first year.
Maximize ROI
Automate routine tasks and refocus resources on high-impact projects.
83% of customers see meaningful savings, and over half save $100K+ in the first year.
%20(1).avif)
%20(1).avif)
Built for operations, designed for people
Daniel Mahn
Business Logistics
The Gathering Place
Graham Houser
IT Technical Associate and Program Manager
University of Illinois Urbana-Champaign
Roger Long
Transportation Foreman
Cameron University
Ken Sutter
Director of Facilities
The Gathering Place
Built for operations, designed for people
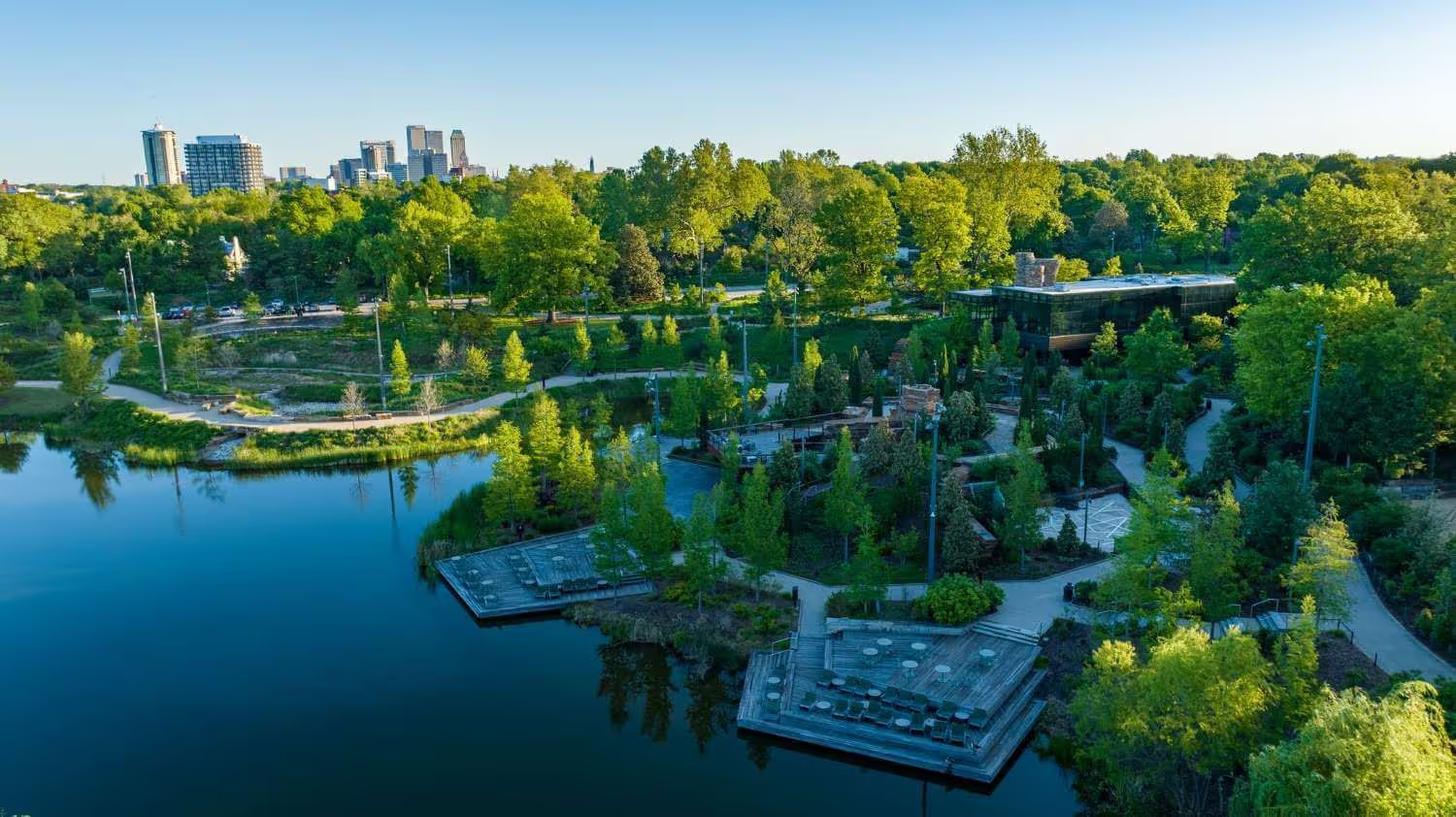
Daniel Mahn
Business Logistics
The Gathering Place
“TMA has offered a great deal to the park. It has allowed us to move from a reactive maintenance approach to a proactive maintenance approach giving us more data on maintenance costs and parts usage.”
.avif)
Graham Houser
IT Technical Associate and Program Manager
University of Illinois Urbana-Champaign
“It’s got a permanent resonance. It provides exactly what we need. It’s part of our business practice. It’s baked in.”
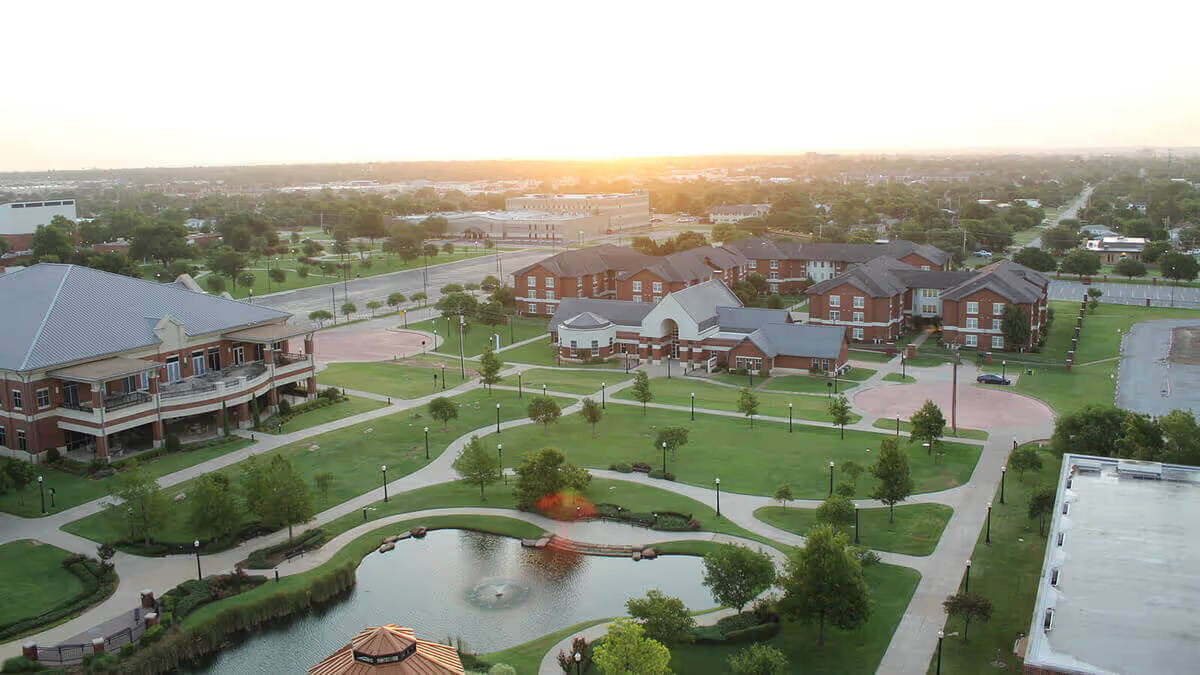
Roger Long
Transportation Foreman
Cameron University
“In this day and age, we are constantly being forced to do more with less and the software enables us to manage and handle a greater number of work requests and problems within our organization with less people.”
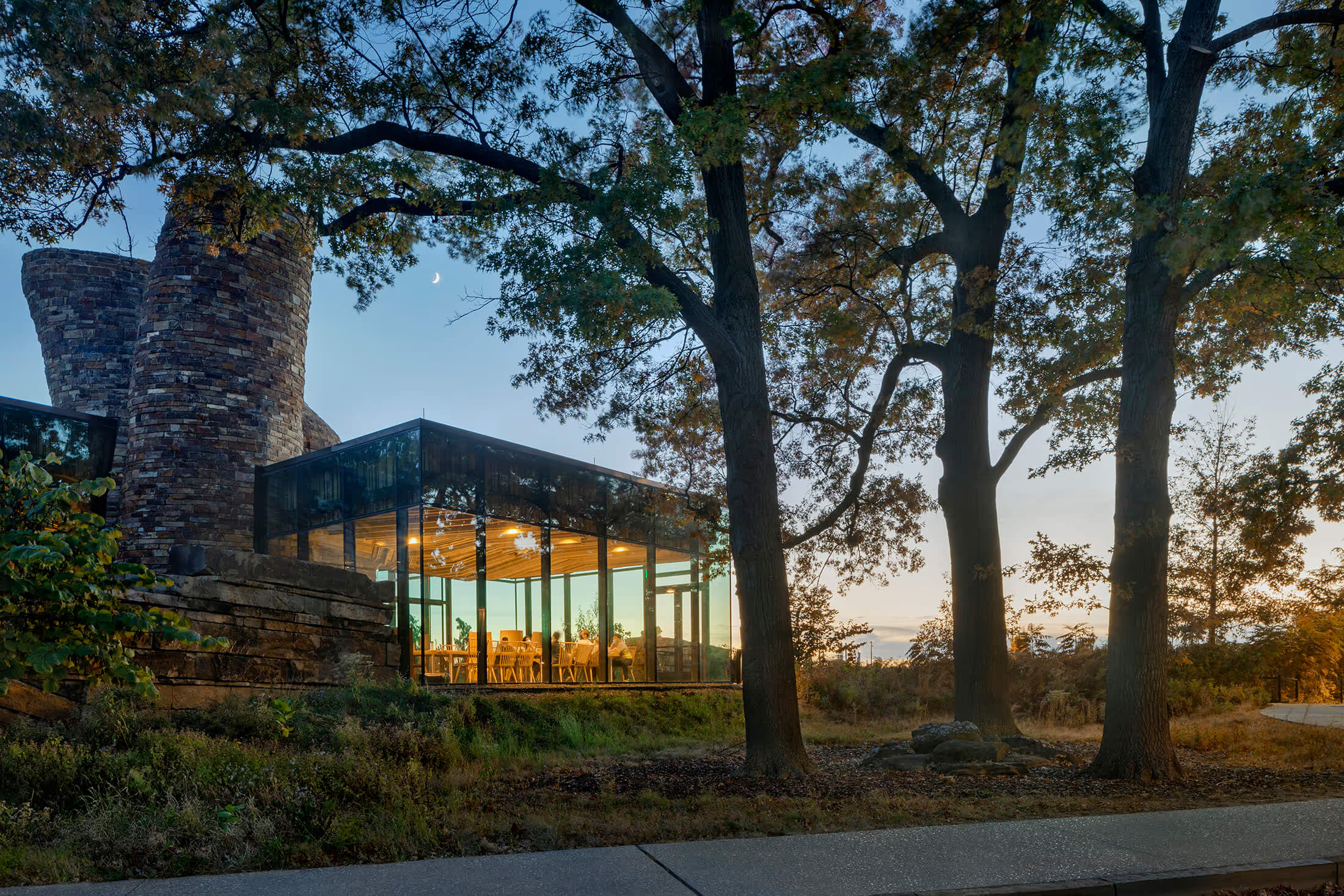
Ken Sutter
Director of Facilities
The Gathering Place
"Our company’s experience with TMA has been stellar. I’ve been involved with other CMMS programs, the user interface is much easier with TMA and the customer support is second to none.”
WebTMA works on the ground & in the field
Give your team the tools to do more in less time. WebTMA streamlines how maintenance gets done, whether you're tracking assets, assigning tasks, or generating reports.
Asset lifecycle management
Track equipment condition, schedule preventive maintenance, and spot issues early to reduce wear, avoid downtime, and extend asset performance over time.
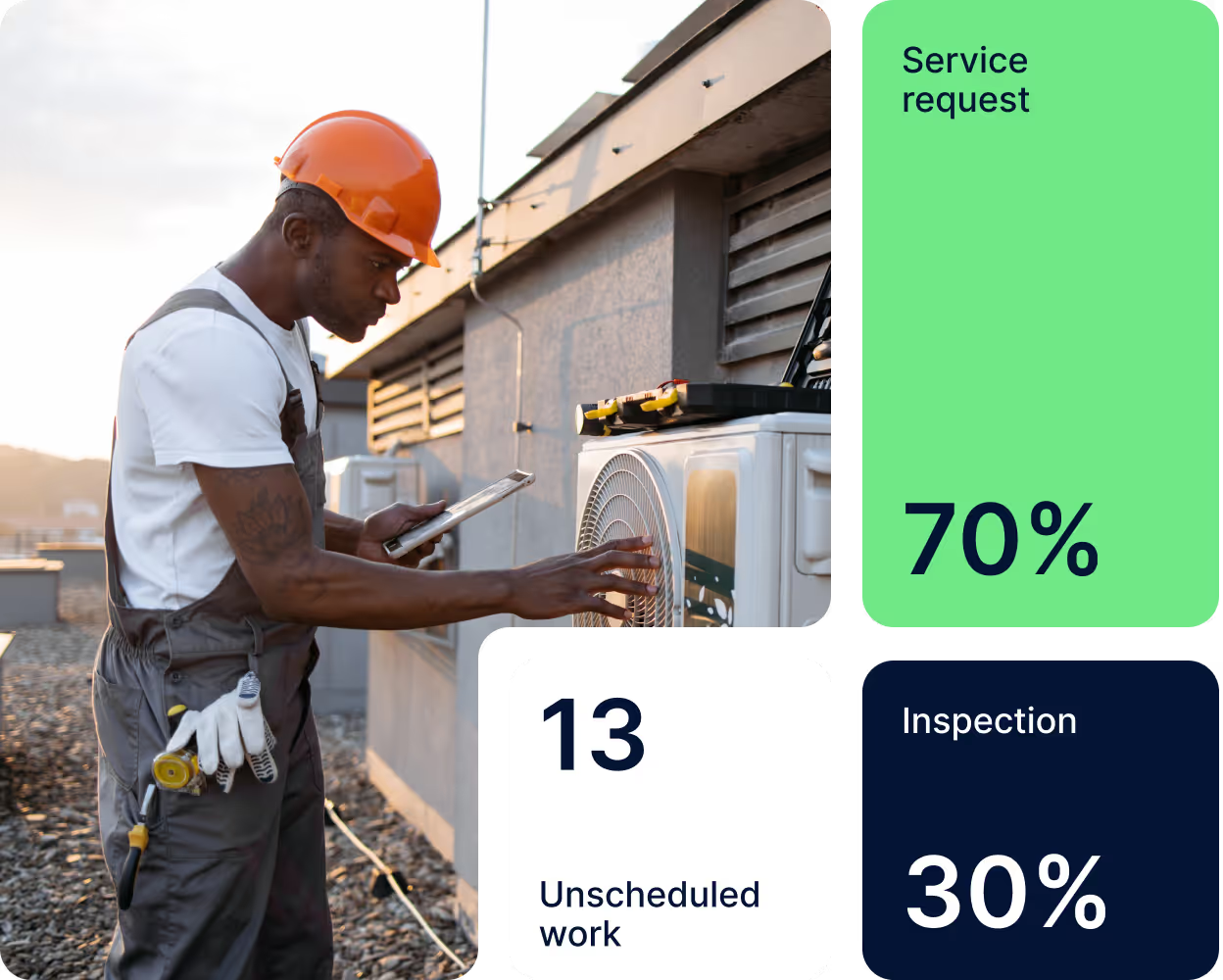
Automated workflows
Build repeatable, rules-based processes that eliminate manual work, reduce delays, and maximize your team’s productivity.
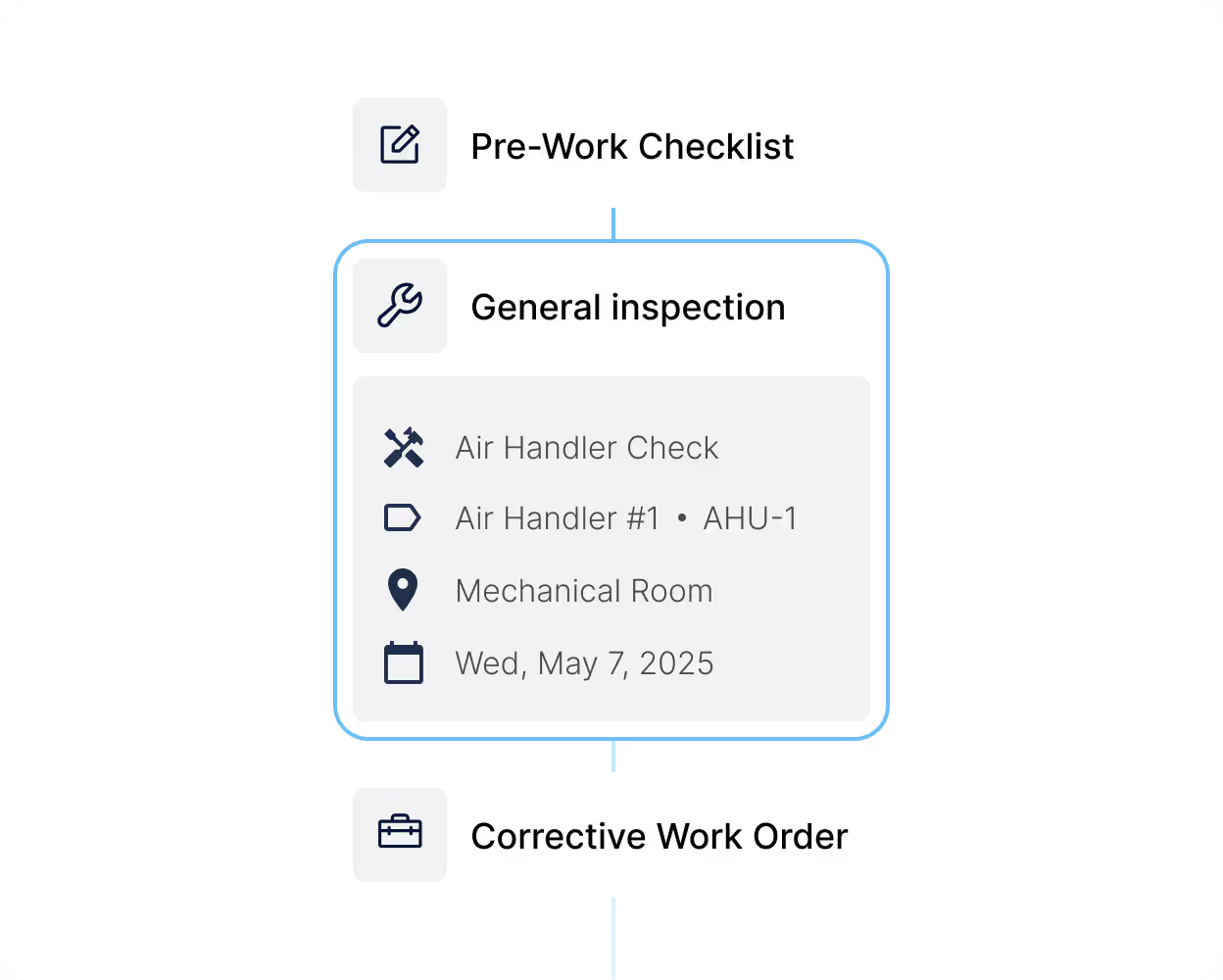
Custom dashboards
& reports
Use centralized data, customizable live dashboards, and built-in reports to uncover trends, prioritize resources, and make smarter, faster operational calls.
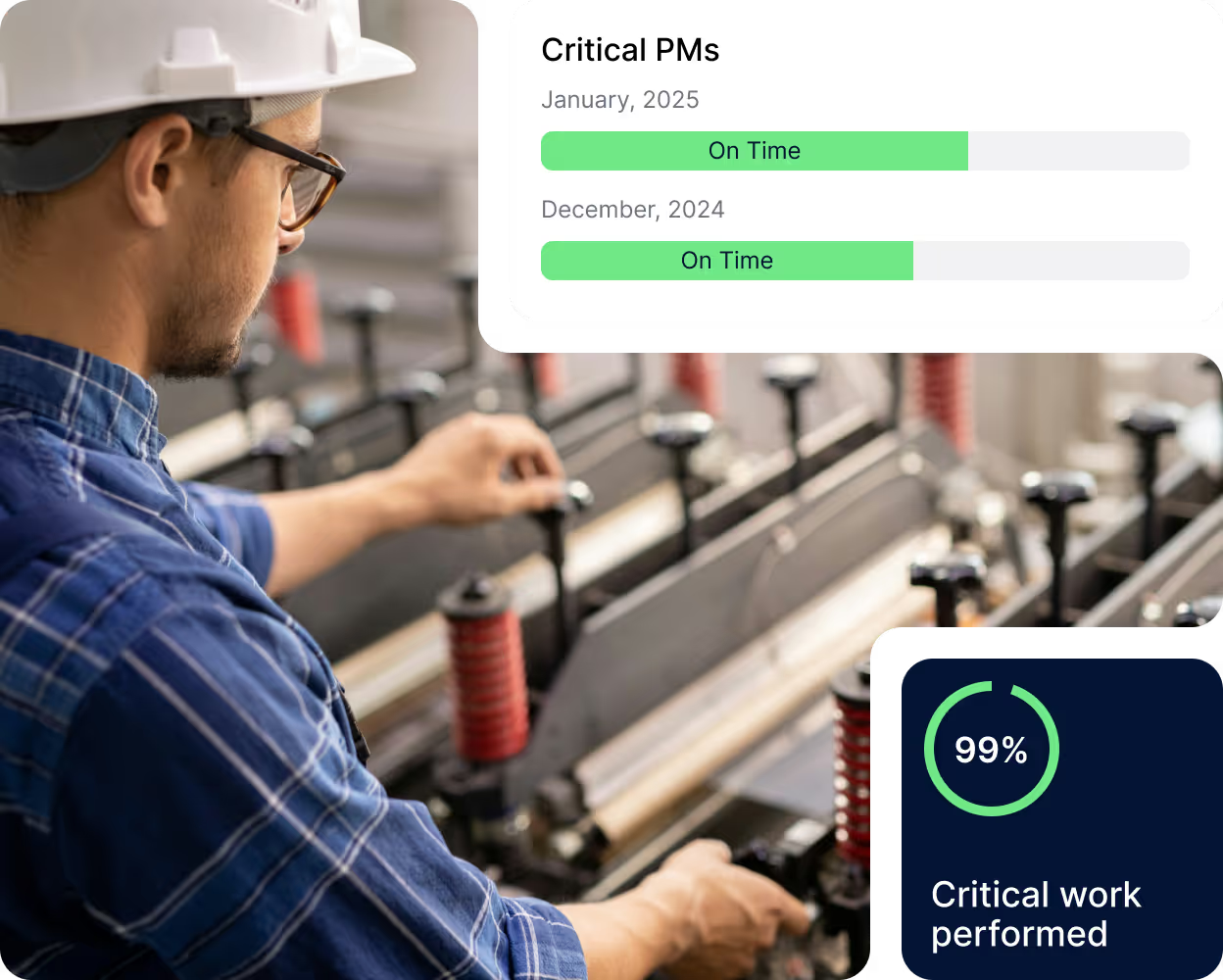
Features that power your workflow
WebTMA handles your day-to-day work and connects your people, assets, and data. Ditch disparate systems—our flexible platform helps you manage assets and facilities maintenance with less friction and more clarity.
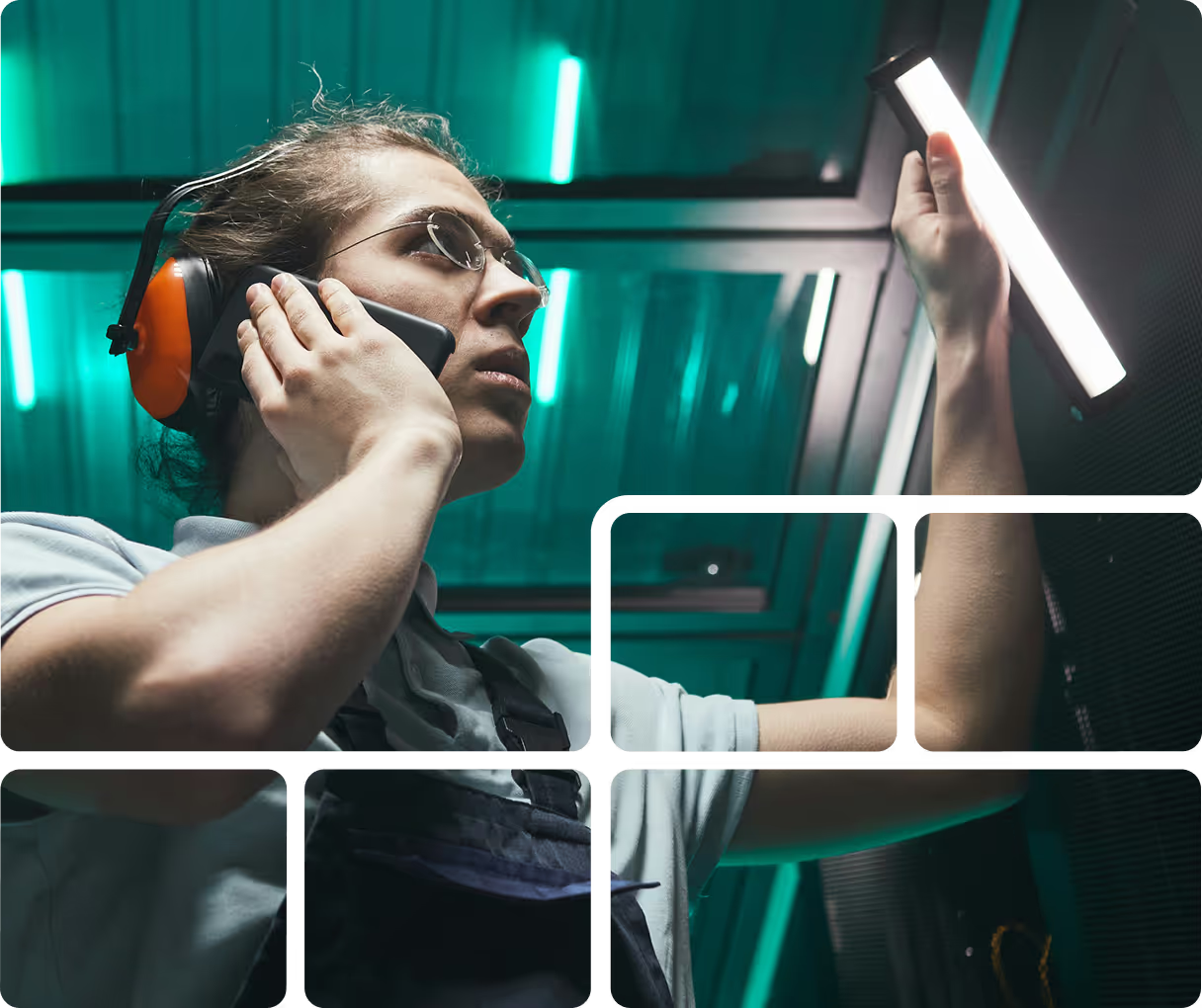
Work orders
Create, assign, and complete work orders with full visibility. Keep teams aligned and tasks moving with built-in tracking for labor, parts, and timelines.
Automated maintenance
Set up recurring tasks, inspections, and preventive maintenance with automated workflows that help reduce downtime and extend asset life.
Service requests
Route service requests efficiently and easily while capturing critical details up front, reducing resolution times.
Lifecycle tracking
Manage assets from acquisition to retirement. Track usage, condition, and cost to make smarter repair-or-replace decisions.
Keep work moving, anywhere
MobileTMA GO puts WebTMA in the hands of your field techs so nothing slips through the cracks.
Scan QR codes & barcodes
Generate work orders
Automate corrective measures
Access cloud storage
Reduce paperwork
Use online or offline
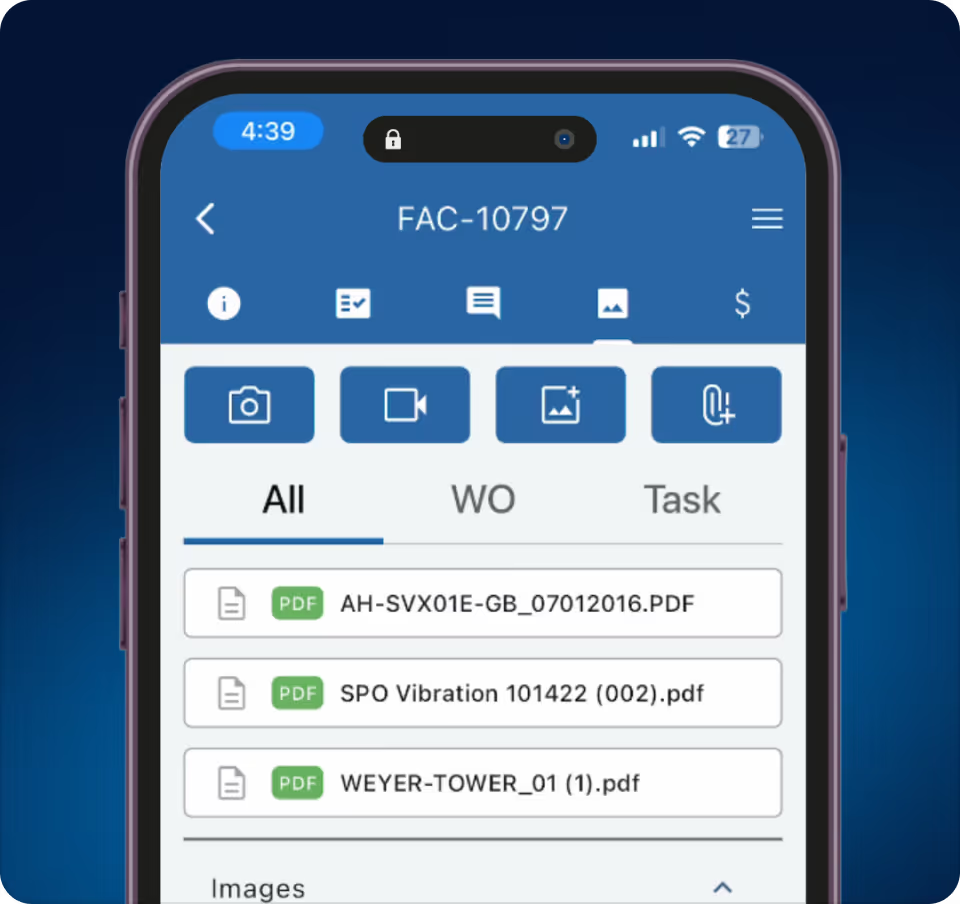
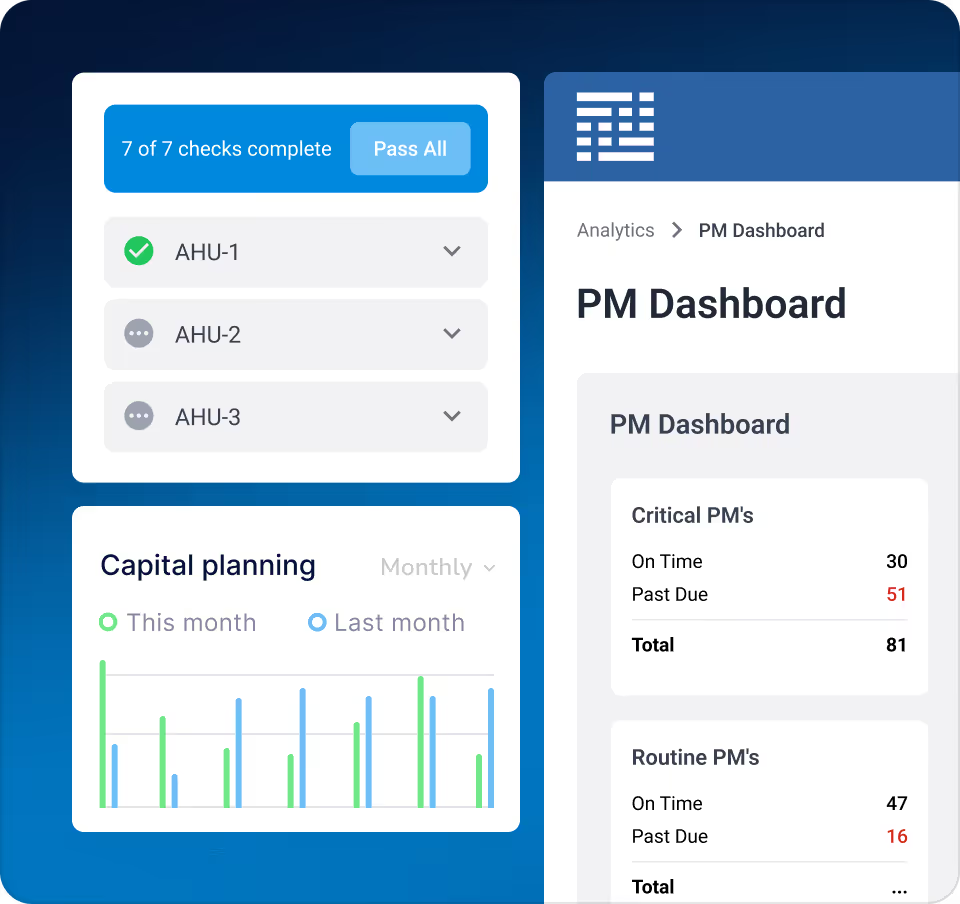
Extend WebTMA’s capabilities
Enhance your system with optional modules and specialized interfaces designed to extend WebTMA’s functionality across departments and workflows.
Capital planning
Executive dashboards
Contract management
General inspections
Event management
Project management
.avif)
See how WebTMA fits into your workflows
Lorem ipsum dolor sit amet consectetur. Eget congue aliquam libero et penatibus. Diam aenean arcu cursus tempus sed maecenas phasellus. Pulvinar enim tristique sed ornare lectus sagittis enim tristique.
Seamless integrations
WebTMA connects with your existing systems to reduce friction, minimize disruption, and improve data flow.
More than just one platform
From SMB and mid-market CMMS and EAM platforms to specialized healthcare solutions, TMA Systems offers purpose-built tools designed to meet different levels of complexity and operational scale.
WebTMA
MEX Maintenance
Eagle CMMS
Explore insights
From scattered tasks to
seamless flow
See how WebTMA connects your day-to-day and helps you shift from reactive to proactive maintenance. We'll walk you through the modules that best fit your goals and show how our onboarding and support make implementation easier.